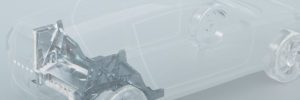
Volvo Cars plans to invest SEK 10 billion ($1.07 billion) in its Torslanda manufacturing plant in Sweden over several years, in preparation for the production of its next generation of EVs. The company will introduce a number of new technologies and manufacturing processes at the plant, including the Tesla-pioneered technique of megacasting of aluminum body parts.
Casting major parts of the floor structure of the car as single large aluminum part reduces vehicle weight and manufacturing complexity.
Volvo also plans to upgrade the Torslanda plant’s paint shop with new machinery and painting processes, which the automaker claims will reduce energy use and emissions. A new battery assembly plant will place cells into modules and packs, and the assembly shop will be modified to accommodate EV-specific processes such as attaching the battery pack to the vehicle structure.
The Torslanda plant, which opened in 1964, has an annual production capacity of 300,000 cars and employs around 6,500 people.
Volvo recently revealed plans for a joint venture with Northvolt, which will invest some SEK 30 billion to build a battery factory near Gothenburg. Construction will start in 2023, and the plant is expected to open in 2025. Annual capacity will be up to 50 GWh—enough to equip 500,000 EVs.
“With these investments we take an important step towards our all-electric future and prepare for even more advanced and better electric Volvos,” said Volvo Cars Chief Executive HÃ¥kan Samuelsson. “Torslanda is our largest plant and will play a crucial role in our ongoing transformation as we move towards becoming a pure electric car maker by 2030.”
“Our future as a company is all-electric and that requires a variety of upgrades across the plant, to ensure that Torslanda can continue to build premium electric cars of the highest quality,” said Javier Varela, Head of Engineering and Operations.
Source: Volvo via Green Car Reports
from Charged EVs https://ift.tt/IsWu4tn
No comments:
Post a Comment