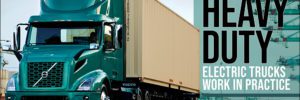
Fleets tested Volvo VNR Electric Class 8 tractors for three years: Here’s what they learned.
Large commercial trucks and other heavy equipment have run on diesel fuel for many decades now. Requirements for more aggressive emission after-treatment and the hardware to achieve that add cost and complexity for fleet operators. Rising fuel-economy standards during the 2020s will do the same. But today, heavy trucks remain a diesel world.
That’s about to change. The far higher volumes of carbon dioxide per mile from heavy trucks make them an obvious target for zero-emission powertrains. Some makers suggest hydrogen fuel cells will be the way to go; the most promising application seems to be long-haul trucking with few or no stops.
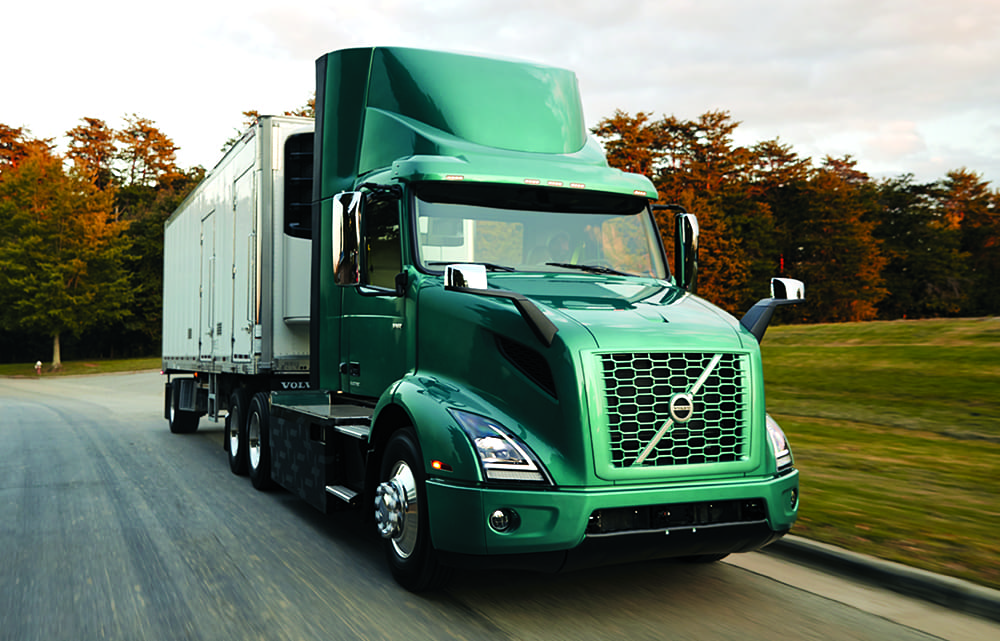
However, heavy-duty electric trucks from traditional makers have started to hit the market. Publicity magnet Tesla said it delivered its first battery-electric Semi tractor on December 1. It has now received a Certificate of Conformity for the Semi from the EPA. Among its first announced customers, back in December 2017, was Pepsi, which reserved 100 of the trucks and plans to use them in the California regions of Modesto and Sacramento.
Volvo Trucks (now a separate entity from the carmaker Volvo owned by China’s Geely) knew several years ago it wanted to get into the electric truck business. Its first model was an electric adaptation of its conventional diesel-powered VNR tractor. It had a 264 kWh battery pack powering the tractor’s twin motors with more than 4,000 lb-ft of torque and a range estimated at up to 150 miles.

To figure out how to make electric trucks work in practice, the manufacturer, the state of California, and a wide array of partners—more than a dozen all told—launched the Volvo LIGHTS (Low Impact Green Heavy Transport Solutions) project in 2019 to test its first electric Class 8 tractors with multiple Southern California operators. The goal was simply to figure out, for a small number of trucks in different uses, what worked, what still needed work, and what practical hurdles existed for battery-electric trucks in a previously all-diesel fleet.
The group’s final presentation lists 18 insights Volvo and its partners gained from the project.
Altogether, the group’s final presentation lists 18 insights Volvo and its partners gained from the project. Many were covered in detail during a day of presentations and site visits for partners and media held this past August in Ontario, California.
New partners for fleets—and lots of them
The overall lesson, repeated frequently, was that multiple entities must come together for electric heavy trucks to succeed—including many that fleet operators haven’t dealt with before—and that this has to happen early in the planning process. Put another way: Plan first, order trucks second.
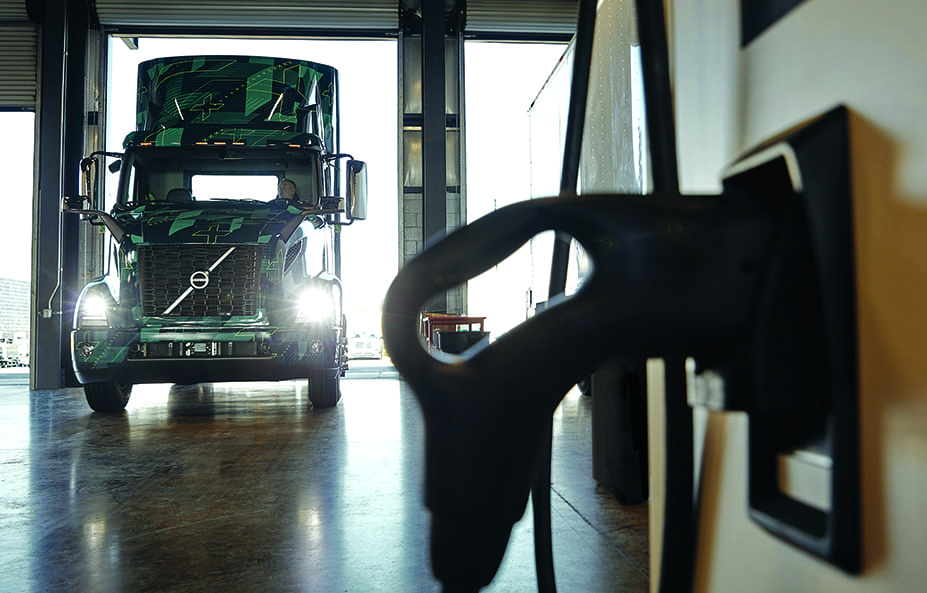
The first lesson, one that may seem obvious, is that electric trucks are better suited to some routes than to others. “Identifying ideal routes is key to success,” says the LIGHTS group’s final report, and the learnings were underscored by the fleet operators taking part.
The starting point was routes of 80 to 150 miles a day, but more factors came into play than sheer range. Topography (lots of hill-climbing or mountainous terrain) and weather (extreme heat or cold) have significant impacts on an electric truck’s effective range. In this case, Southern California has fairly temperate weather, and parts of the region are quite flat. But the fleet operators need to work together with the truck-maker and its dealerships to identify the most promising initial routes for electric trucks.
Driving style also matters. Experienced diesel drivers will need training for electric trucks to maximize use of regenerative braking, which can recapture 5 to 15 percent of a battery’s energy.
Driving style also matters. Experienced diesel drivers will need training for electric trucks to maximize use of regenerative braking, which can recapture 5 to 15 percent of a battery’s energy. While semi drivers can be a conservative group, those willing to become the first EV drivers in their fleets soon came to appreciate some side benefits of electric trucks.
Driver Elvis Alvarado and fleet manager Hector Banuelos openly discussed the pros and cons of the first-generation VNR Electric tractor tested by NFI. Among its advantages were smooth power delivery, lack of continuous gear shifting, less vibration (“I could write on my notepad,” marveled Alvarado), and the ability to retain cabin cooling or heating when parked in no-idle zones. Also, he noted, he needed much less time to check over the truck’s powertrain before runs—and he didn’t smell like diesel fuel after the workday.
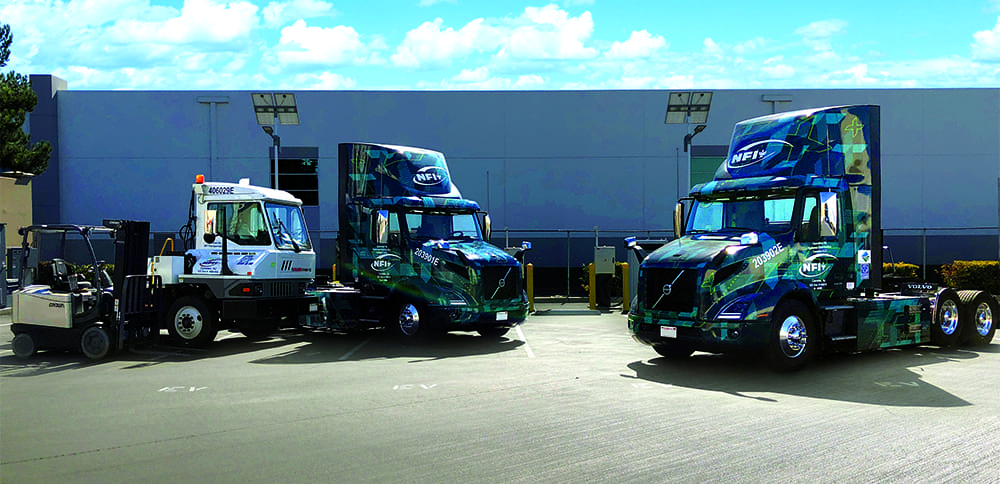
As for challenges: The VNR Electric tractors were quiet enough that yard and port staff often didn’t hear them coming, requiring extra alertness on the driver’s part. Range anxiety was a continual factor, and Banuelos suggested it could be hard to get the quoted 150 miles to cover two round trips to a port and back in a 10-to-12-hour shift. He expects the 250-mile range of second-generation VNR Electric tractors to provide a comfortable margin in many more circumstances.
Dedicate a project manager to EVs
It’s crucial that any operator have at least one person charged with the responsibility of coordinating all aspects of adding electric trucks to a fleet. He or she should be prepared to work closely with primary contacts at the electric utility, perhaps multiple government agencies, any contractors hired to upgrade electric service or install charging equipment, and more.
It’s crucial that any operator have at least one person charged with the responsibility of coordinating all aspects of adding electric trucks to a fleet.
While a truck-maker and its dealer can help in identifying suitable routes and matching them to electric trucks, that’s only the start of the process. Shepherding the planning, permitting and construction of the needed infrastructure, training for fleet operators and drivers, and ensuring that trucks don’t arrive until their charging is live…all of those tasks should be centralized in one person with clear authority and lines of reporting.
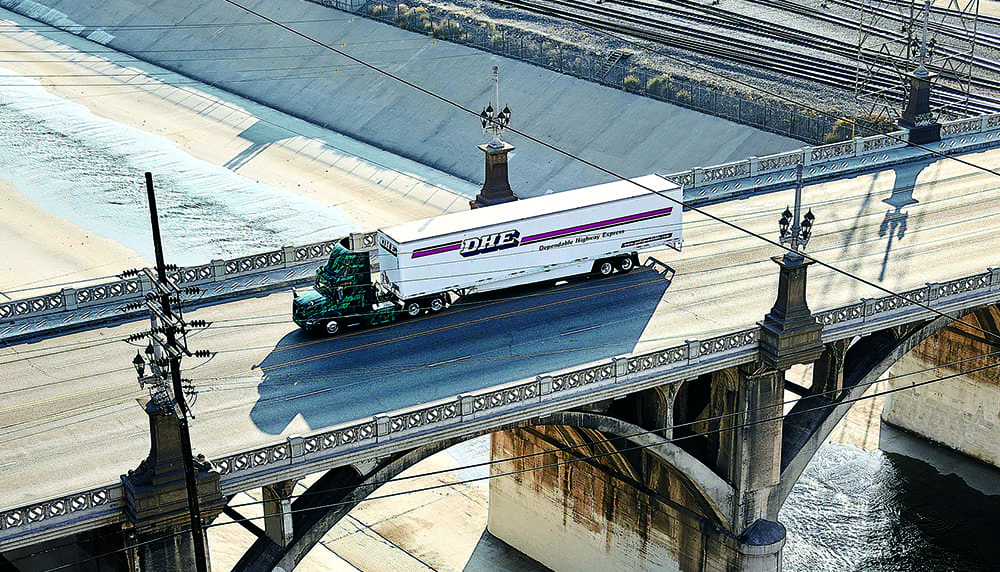
It can well become a big, complicated, sprawling job. But for ambitious fleet staff, it’s experience that can make them far more attractive to future employers.
Charging infrastructure installs vary, a lot
Electricity is everywhere, including in or near the fleet depots and parking lots where heavy trucks spend much of their time. But the time and cost of installing the needed charging infrastructure for electric trucks can vary enormously: “from a few thousand dollars for lower-power chargers to millions of dollars for high-power chargers” that can deliver up to 1 megawatt each.
The time and cost of installing the needed charging infrastructure for electric trucks can vary enormously.
It’s hard to generalize on costs and effort, but factors include a fleet’s electrical load profile (how much power needs to be delivered, and when), the size and cost of the chosen charging hardware, the existing electrical infrastructure at the sites chosen, and even the distance of a site from high-voltage service lines.
One major tradeoff is what level of DC fast charging is required to allow trucks to fulfill their duty cycles. A 150 kW charger may recharge a battery pack to 80 percent in about 2.5 hours, while a 250 kW unit can cut that to 1.5 hours—at the cost of longer installations, more infrastructure work, and higher charging station costs. It all depends on the needs of the routes being covered by the electric trucks.
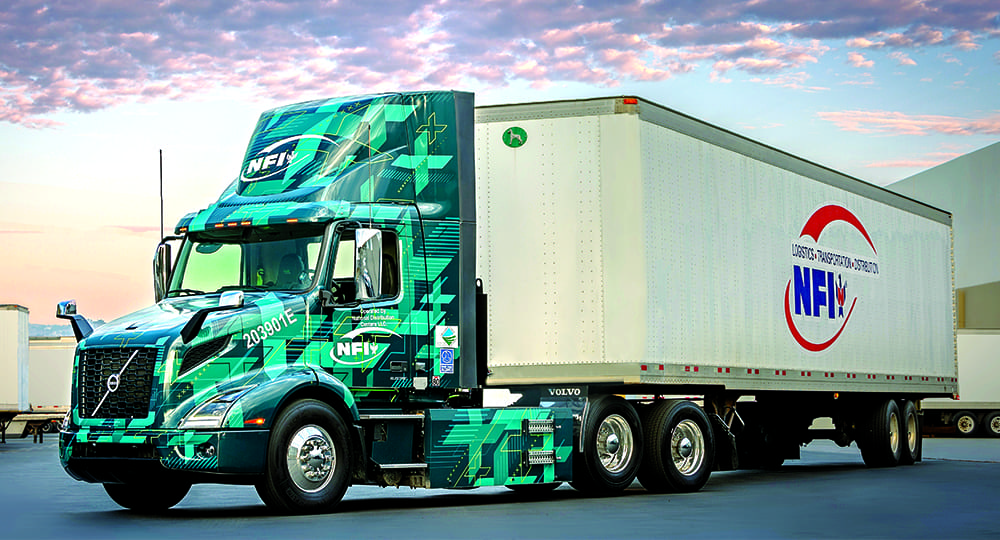
As the report notes, “A more powerful charger may entail longer installation timelines and higher capital investment costs in the form of civil and electrical upgrades that are difficult to justify during an early demonstration stage but can provide a faster charging experience.”
Faster charging is typically more expensive because it requires an electrical system to operate at peak power, for which utilities levy higher demand charges, since it puts more stress on the electric grid. However, these higher energy costs can often be managed through a sophisticated EV service platform for smart charging.
For fleet operators, concepts like demand charges and charging management software are entirely new. When it comes to diesel fuel, the only significant variables are how far away it is and what it costs per gallon. The small number of operators who run mixed-fuel fleets (diesel and gasoline, or diesel and natural gas) will understand these tradeoffs better.
It’s crucial to plan for future upgrades—by wiring for higher power or more stations than needed at launch—to prevent the need to retrench and add wiring down the road.
Starting out, fleets may want to mix high- and low-power DC fast charging to see which meets the needs of different duty cycles and routes. But if asphalt must be trenched, electrical service must be upgraded, and new cabling must be run into parking lots, it’s crucial to plan for future upgrades—by wiring for higher power or more stations than needed at launch—to prevent the need to retrench and add wiring down the road.
Expect the unexpected, plan on delays
With luck, not every electric truck launch will take place amidst a global pandemic, as the Volvo LIGHTS project did. But the process of installing charging infrastructure will inevitably encounter delays, as all the participants stressed. The earliest possible contact with both the electric utility and local land-use and permitting authorities is crucial, especially if this is the first local project with megawatt-scale charging.
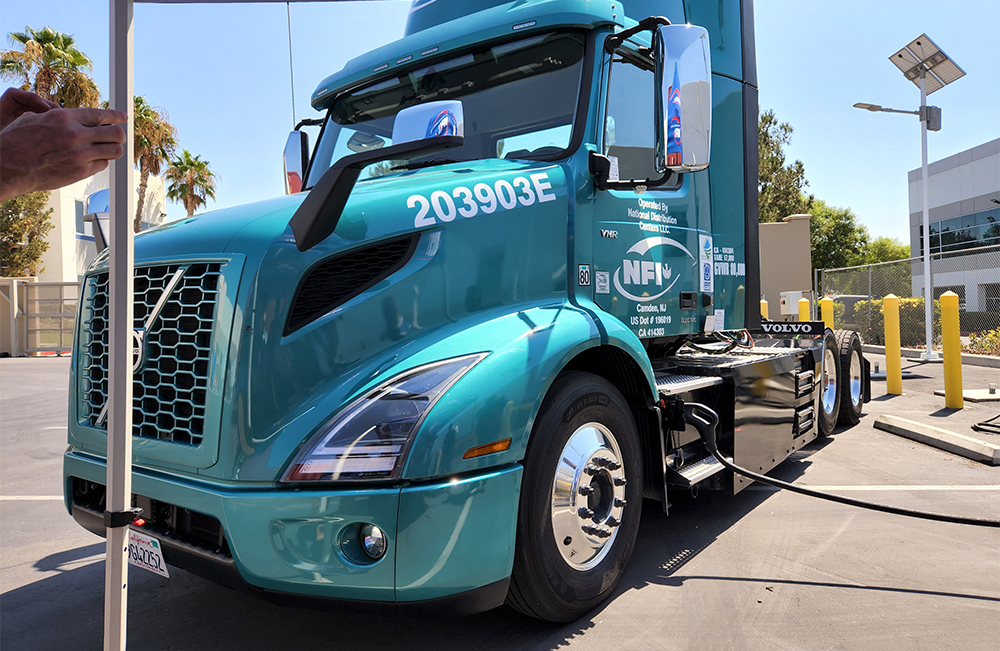
Those early meetings will help “calibrate expectations” for the fleet operator about how fast a project can realistically progress. The LIGHTS partners advised EV fleet adopters to build in extra time before the vehicles themselves are scheduled to be delivered—because a large electric truck without the ability to charge it is little more than a parking-lot paperweight.
Emissions come way down, and so does cost, but …
There’s no longer any question that electric trucks have significantly lower lifetime carbon footprints than any trucks running on fossil fuel. Furthermore, like passenger EVs, their carbon emissions per mile will fall over their lifetimes as the grids they’re charged on decarbonize.
The LIGHTS team had the Volvo VNR Electric tractor assessed by a team at the University of California, Riverside on a heavy-duty dynamometer. Combined with a life-cycle assessment (LCA) of the electric truck’s well-to-wheel impact, the Volvo VNR saved 65 percent of total energy and 81 percent in fossil energy, and it cut lifetime greenhouse-gas emissions and criteria pollutants (hydrocarbons, nitrogen oxides, carbon monoxide and soot) by more than 80 percent compared to a baseline diesel truck.
The cost equation is trickier. Today, battery-electric Class 8 tractors still have a higher lifetime cost, due entirely to the initial purchase price of a heavy-duty vehicle with a huge battery (264 kWh for the first-generation VNR Electric). An electric Class 8 tractor still carries roughly twice the price of a comparable diesel version. That in turn raises insurance costs as well. The LIGHTS team found that, once acquired, the electric truck had significantly lower operating costs per mile—but that didn’t make up for the higher purchase cost.
The LIGHTS team found that, once acquired, the electric truck had significantly lower operating costs per mile—but that didn’t make up for the higher purchase cost.
Several speakers highlighted the need for more federal, state and local incentives to encourage use of zero-emission heavy trucks.
From the report: “The federal government and some states offer dedicated grant programs for BEVs and related infrastructure, but the funding currently available isn’t sufficient to support widescale market deployment. In California, several utilities offer incentive programs to buy down the capital equipment cost for their customers, a model other states should consider emulating.”
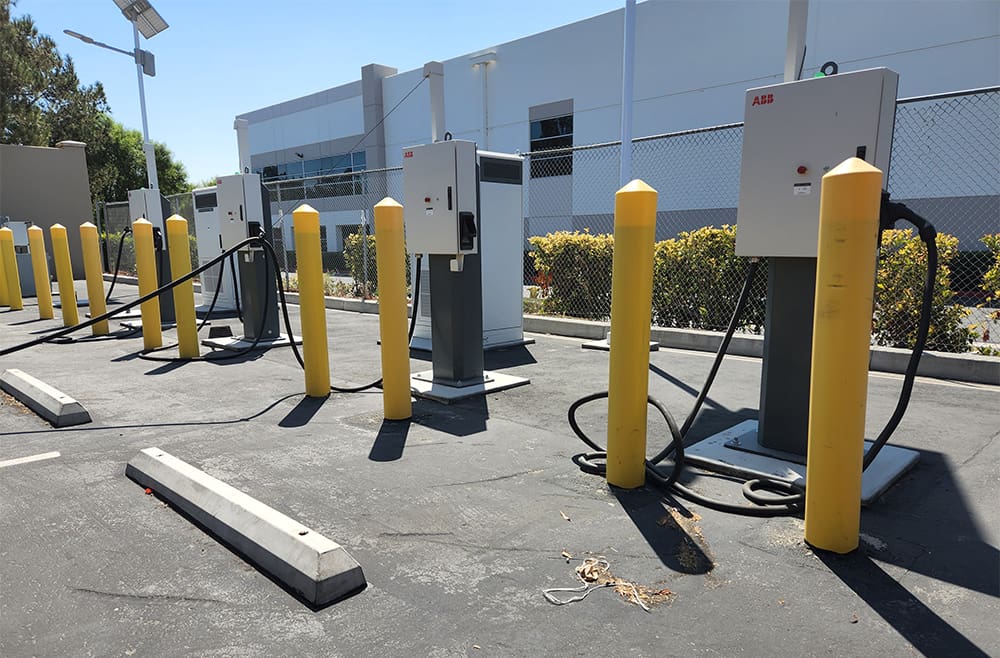
Onward and upward
Now that the Volvo LIGHTS program has officially concluded, what’s next? Volvo has launched an updated version of its VNR Electric truck, with increased ranges of up to 230 or 275 miles from battery packs of 375 and 565 kWh. Those trucks are now arriving at selected dealers in California and elsewhere. The company expects to sell hundreds of them, which will provide more real-world experience in a broader array of use cases.
Moreover, to expand beyond depot charging—the focus of the LIGHTS project—Volvo Group announced in mid-November that it would partner with the Pilot Group. That company, which operates more than 750 Pilot and Flying J travel centers across North America, plans to install high-performance charging infrastructure at selected locations over the next few years. This is a step that, so far, Tesla has not taken for its own Megacharger standard.
Mack Trucks, also owned by Volvo Group, updated its own electric tractor in March. The latest Mack LR Electric uses a standard 376 kWh battery, with twin electric motors producing 330 kW (448 hp) and identical peak torque to the VNR Electric. The Mack electric truck is part of a $10-million program by the New York State Energy Research and Development Authority (NYSERDA) to reduce emissions by using zero-emission trucks in the Hunts Point neighborhood of the South Bronx, which suffers from some of the worst air quality in New York City.
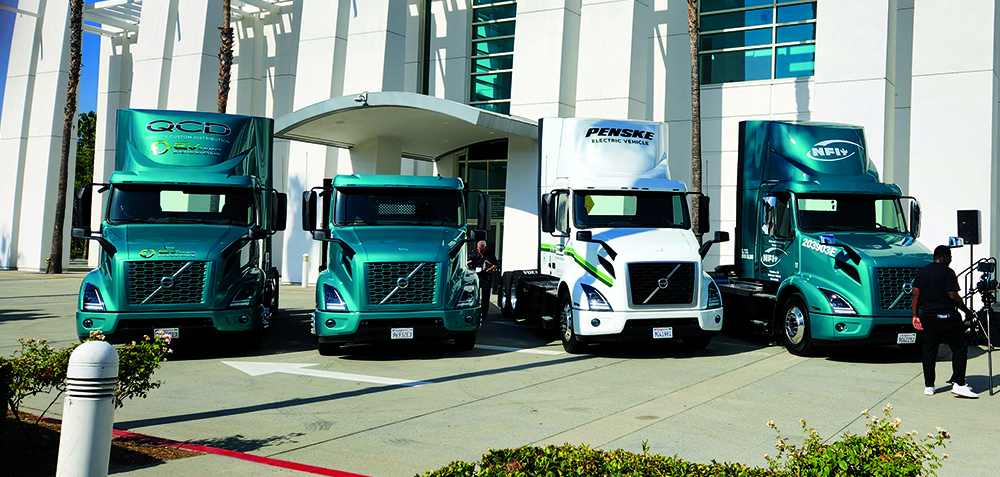
Meanwhile, participants in the LIGHTS Project expect to continue experimenting with electric trucks. They’ve seen some of the pitfalls, understand the process better, and are now considering how those experiences will let them scale from one truck to, say, ten, and then more. Stay tuned.
This article appeared in Issue 62: Oct-Dec 2022 – Subscribe now.
Participants in the Volvo LIGHTS Project were: California South Coast Air Quality Management District, Volvo Group, Dependable Supply Chain Services, trucking fleet NFI, the Ports of Los Angeles and Long Beach, Southern California Edison, TEC Equipment, Shell Recharge Solutions (née GreenLots), University of California, Riverside College of Engineering, Rio Hondo College, San Bernardino Valley College, Reach Out and Calstart.
Funding of $90 million for the project came from the California Climate Investments, which contributed $44.8 million of Cap-and-Trade money. The balance came from the project partners.
Volvo Trucks provided airfare, lodging and meals to enable Charged to bring you this first-person report.
from Charged EVs https://ift.tt/EpDX0Im
No comments:
Post a Comment