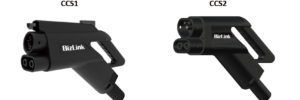
With the converging automotive trends of vehicle electrification and Advanced Driver Assistance Systems (ADAS), the role of traditional automotive interconnects is evolving to meet more demanding performance requirements for key automotive application areas, including high-power interconnects specific to electric vehicles, and high-speed data interconnects required for ADAS control components which will ultimately evolve to fully autonomous vehicle systems.
The next generation of high-power automotive interconnects include those for vehicle batteries/drive trains, and other internal systems; as well as external connectors for EV charging stations designed to handle the larger vehicle batteries with higher amperages that deliver faster charging speeds.
Advanced interconnects and wiring harnesses will be required to handle significantly increased bandwidth, multiple sensor inputs from cameras, LiDAR, and radar devices, all at higher data transfer speeds with more complex network architectures needed for ADAS and autonomous vehicle systems.
Internal High-Power Interconnects
Power connections internal to the vehicle deliver electric current from the charging inlet to the vehicle battery and distribute the battery power to the vehicle’s drive train and other systems, such as inverters, motors, and auxiliary devices. The internal wiring scheme of an all-electric vehicle typically requires tear-resistant silicone-jacketed cables that are resistant to the harsh conditions, abrasion, fluid exposure, and chemicals present in automotive environments. Cables for the vehicle’s internal power connection typically range from 10mm to 40mm in diameter, rated to the LV 216-1/2 standard for sheathed high-voltage power transmission. These cables and the connectors require a wide temperature range from -60°C up to 150/180/200°C (upper temperature limit is dependent on the location within the vehicle). The connectors must be designed so that the cable bend radius is as small as possible to limit the mechanical stress to the cabling.
https://www.bizlinktech.com/products/index/240/Motor+Vehicle
External Charging Connectors
DC (direct current) fast charging is essential for providing drivers with a method of charging electric vehicles in a short period of time. This applies for long-distance driving for single vehicles as well as charging large fleets of EVs efficiently. Traditional EV charging using AC power often required overnight charging.
Older electric vehicles were typically limited to a maximum charge of 50kW, but newer model EVs with larger batteries can accept a charge from stations rated at 270kW or even 350kW. Therefore, the charging connector for new designs must be rated to handle this higher power.
Compliance with North American and European DC fast-charging automotive interconnects must meet the UL 2251 and IEC 62196 standards established for electric vehicle charging systems. These standards are CCS-1 (North America) and CCS-2 (Europe) that are air-cooled charging connectors rated to 300A DC current, and liquid-cooled CCS-1/2 devices rated for a minimum 500A DC.
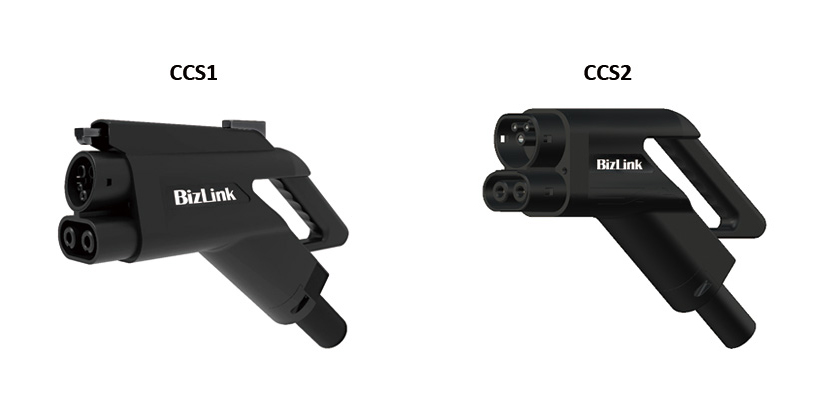
High-Speed Interconnects for ADAS and Autonomous Vehicle Systems
Increased bandwidth and data transmission speeds are required for the next generation of advanced driver assistance systems, including vehicle safety devices such as sensors, cameras, radar/LiDAR, and telematics, as well as infotainment and other non-safety systems. The coaxial cables and interconnect wiring harnesses for these multiple sensors must have increased data capacity and transmission speeds to support the volume of this sensor data, especially as the automotive industry transitions from driver assisted systems to fully autonomous vehicles.
One standard automotive interconnect system involves the FAKRA (Fachkreis Automobil) connector family, developed to meet the stringent mechanical and environmental requirements of the automotive industry. These connectors are available in multiple configurations and feature keyed with color-coded designs for easy identification and to prevent mis-matching, with primary and secondary locking systems for secure connections. Rated for data speeds up to 8Gps, these connectors are ideal for developing wiring harnesses for high-speed one-way data transfer from sensors located within the vehicle, including cameras, GPS navigation, infotainment, RF keyless entry, and driver comfort systems.
For safety-critical connections that require higher speed data transfer rates, wiring harnesses using the mini-FAKRA interconnect series supports up to 28Gbs data transmission. In addition to the higher data speeds, the mini-FAKRA connectors are 80% more compact than standard FAKRA connectors, saving space and weight in vehicle electronics systems. Wiring harnesses using these connectors are ideal for autonomous driving and critical driver assistance systems, as they can deliver high data volumes from multiple sensors, cameras, and navigation sources.
Zonal Control Architecture to Support Autonomous Vehicles
Traditional automotive electrical/electronic systems use a domain-based architecture, with specific modules, devices, and sensors wired to central ECUs (electronic control units). This approach can only scale up to a certain point before reaching limitations based on size, weight, and data transfer speeds.
Newer automotive systems feature a zonal architecture using Ethernet cable specifically designed for automotive applications. Replacing the individual wires and nodes is an Ethernet backbone that connects all the vehicle’s systems with a software-controlled network that is capable of aggregating and transmitting data from different nodes within the vehicle, using a common protocol to support different data speeds to deliver signals to different computing locations onboard the vehicle. This zonal approach uses Ethernet switches, or gateways, at each system node to manage the increased data streams required for advanced vehicle systems, and enables local computing for less time-sensitive processing while routing time-critical safety/control systems to be channeled to the central high-speed vehicle computers.
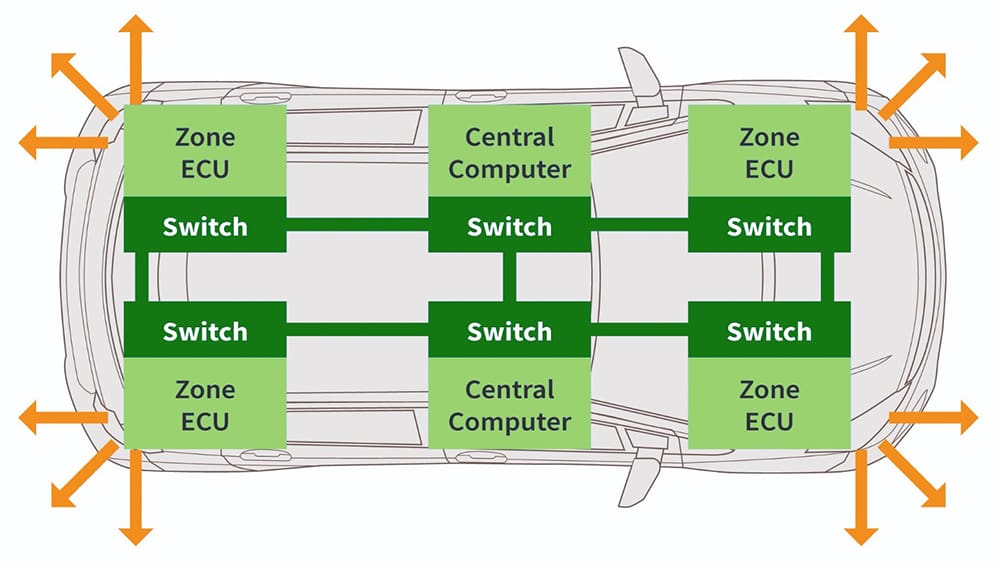
This type of zonal architecture requires the use of differential wiring harnesses and cable assemblies using Automotive Ethernet cable with data transmission rates up to 25Gbps, as well as the connectors to link with each node on the vehicle network. These cables must meet the OPEN alliance standard TC2/9 established for Ethernet communications on vehicles.
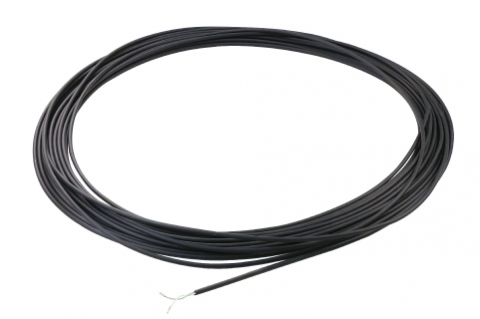
With the increasing number of electric vehicles and vehicles with advanced driver assist systems, the need for high-speed, high-density power and data transmission is quickly outpacing the traditional systems for internal vehicle wiring and external EV charging.
Because each electric vehicle model has its own unique design requirements and cost constraints, automotive designers should select a cable assembly/wire harness partner with global operations capable of applying a wide selection of connectors, cable, and charging components to meet individual customer vehicle design requirements. It is also critical that all wiring components are manufactured in ISO/TS 16949 and IATF 16949-certified facilities with automotive quality certifications, including ISO 9001, ISO 4001, OHSAS 18000, and UL.
BizLink continuously strives to advance its ODM/OEM interface capabilities and to develop innovative, high-performance interconnect solutions and technologies that meet the industry’s growing demands. For more information, visit BizLink’s website.
from Charged EVs https://ift.tt/7zWjCLo
No comments:
Post a Comment