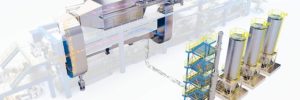
The Dürr Group, a global mechanical and plant engineering firm, is expanding into battery production. Now the company is delivering a technology for sustainable battery manufacturing to CATL, which the Chinese battery manufacturer will use at a new plant currently being built in Arnstadt, Germany.
The order comprises several systems based on an eco-friendly process for solvent recovery in battery production. Dürr’s technology enables the solvent to be reused multiple times, significantly reducing CO2 emissions and costs.
In battery factories, solvents are used in the coating of electrode foil. In Arnstadt, CATL plans to run multiple coating lines, each of which will be equipped with a Dürr system for solvent recovery. Dürr’s Sorpt.X LC technology, in combination with a distillation system, is designed to allow over 95% of the recovered solvent to be reused at the required quality.
Dürr’s process uses the solvent N-Methyl-2-pyrrolidone (NMP) to dissolve the active materials employed in electrode coating. NMP is classed as a hazardous substance, and furthermore, it is not cheap—around €3,100 per ton, according to Dürr. The company’s Sorpt.X LC solvent recovery system removes solvents from the exhaust air of electrode coating systems, while recovering the heat and 99.9 percent of the NMP.
“Our technology will make a major contribution in helping CATL produce its electrodes in a way that is both sustainable and economical,” said Dr. Jochen Weyrauch, CEO of Dürr. “The production processes [battery factories] use ultimately play a critical role in determining the size of an electric vehicle’s environmental footprint.”
Source: Dürr via Battery Tech News
from Charged EVs https://ift.tt/VCwZefW
No comments:
Post a Comment