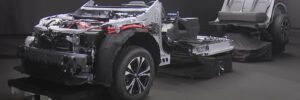
It’s been a long time since auto industry observers have seen Toyota as an innovator, so it was a pleasant surprise when the world’s second-largest automaker demonstrated a version of the die-casting process pioneered by Tesla, using a massive hydraulic press to cast the entire rear third of an auto chassis as a single piece.
As reported by Nikkei Asia, this chassis section could replace an assembly that’s currently made up of 86 individual parts in a 33-step process. Among other benefits, this could reduce production time for the part from several hours to three minutes.
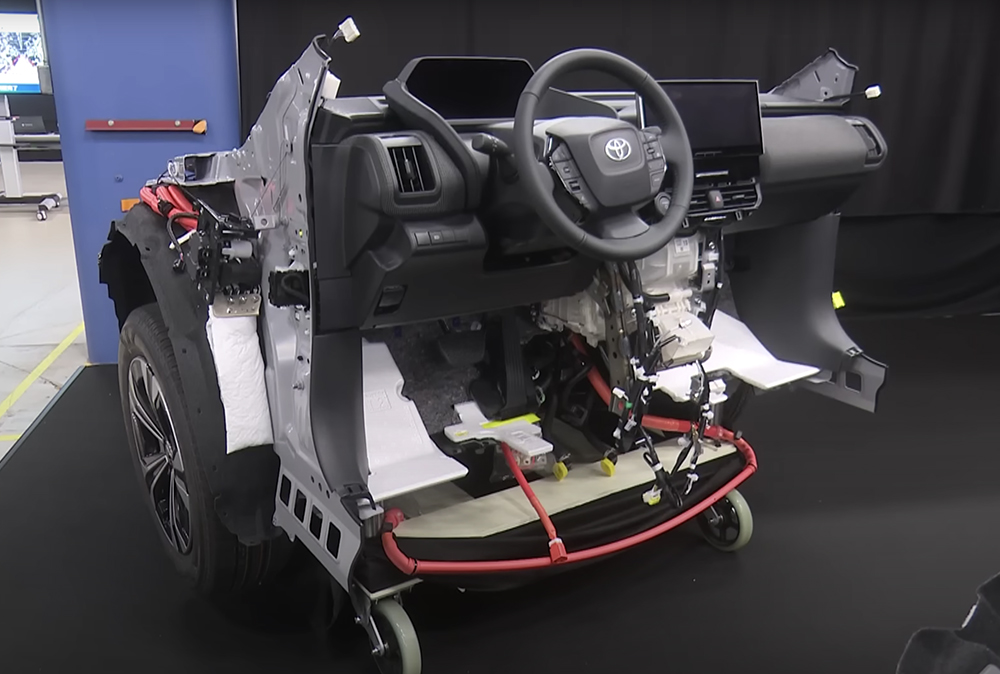
Toyota hopes the die-casting process (or gigacasting, to use the term coined by Tesla), combined with other production advances, will reduce total assembly times by 50%. The carmaker plans to show off some of its new processes and technologies in a concept EV at next month’s Japan Mobility Show, and says it will use gigacasting to make the front and rear sections of a new EV due out in 2026.
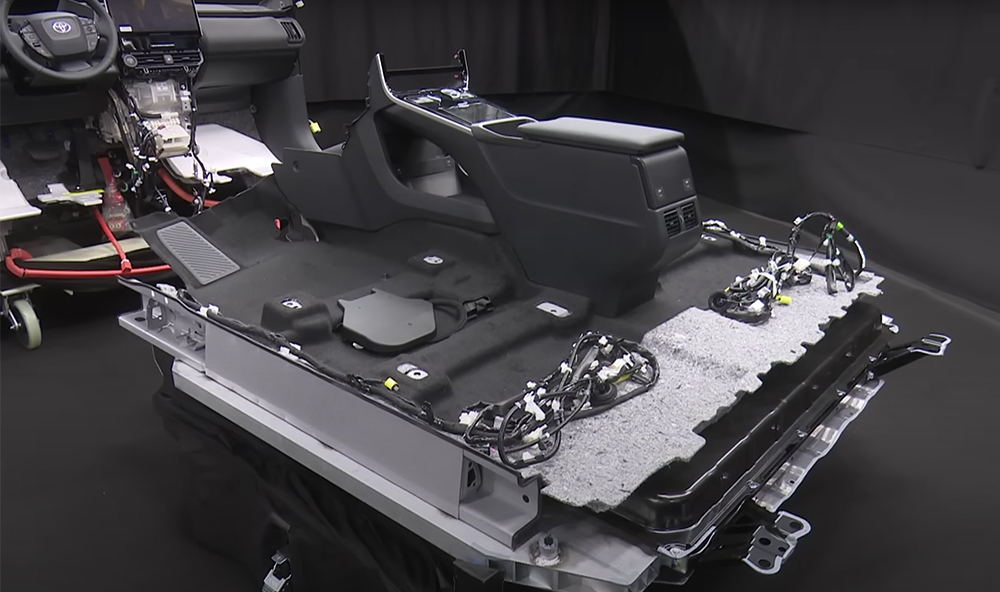
Tesla’s gigacasting technique uses giant casting machines to make car bodies with just a few massive cast parts, saving costs and improving efficiency. The company began using it to produce Model Y in 2021. Soon after, several Chinese companies placed orders for gigapresses with the LK Group. Hyundai and Volkswagen are also said to be investigating the technology.
Did the recent news that Tesla is outselling Toyota in California apply some heat to the Japanese automaker’s corporate posterior? The closest thing to such an admission we’re likely to hear is this coy statement from Chief Production Officer Kazuaki Shingo: “We’re learning new options from specialized EV makers to take on the challenge” of electrification.
Source: CarBuzz, Nikkei Asia
Photos courtesy of Toyota
from Charged EVs https://ift.tt/hNwTRkP
No comments:
Post a Comment