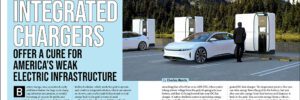
Q&A with Alex Urist, Vice President of XCharge North America
Battery storage, once considered a nifty additional feature for large-scale charging infrastructure projects, is steadily becoming de rigueur for public and commercial charging deployments of all sizes. Adding batteries to the system offers several benefits: coupled with on-site generation, it allows charging to be offered at off-grid locations; it enables peak shaving to avoid utility demand charges; and in some cases it allows a site to avoid expensive grid connection upgrades.
XCharge considers battery storage to be an integral component of a charging site. Furthermore, the company draws a distinction between a battery-buffered solution, which needs the grid to operate, and a battery-integrated solution, which can operate on its own, and can be made bidirectional to send energy back to the grid in times of need.
Alex Urist, Vice President of XCharge North America, explained to Charged how its solutions are specifically tailored to the American electrical grid.
Charged: So, the difference between a mere battery-buffered charger and a battery-integrated charger is flexibility?
Alex Urist: Absolutely. What’s generally out there in the wild now is a battery-buffered system—something like a FreeWire or an ADS-TEC, where you’re taking a lower voltage from the grid, it’s going into your battery, and then it’s being boosted into your DC fast charger. A battery-buffered system is just taking energy from the grid. There’s no component of bringing that energy from either the car or from the battery back to the grid.
A battery-buffered system is just taking energy from the grid...But a battery-integrated system has a little bit more flexibility in its usage, because the battery can function separately from the charger applications.
When we think about the ability to buffer charging, that’s obviously a key and integral component of the unit—it requires less of a grid connection. But a battery-integrated system has a little bit more flexibility in its usage, because the battery can function separately from the charger applications.
What we manufacture is a bidirectional battery-integrated DC fast charger. The important point is that you can take energy from the grid to the battery, but you also can take energy from that battery and dispense it back to the grid. You can take energy from a vehicle, dump it into a battery, and it can be held in the battery either for charging other vehicles with the operator taking an arbitrage off of the pricing, or that energy can be placed back into the grid for arbitrage opportunities, resiliency, you name it. Looking forward, that can also apply to V2X applications. There’s also the benefit of being able to take energy from photovoltaics, store it in the battery, and then sell that energy back to the grid or use it to charge a car.
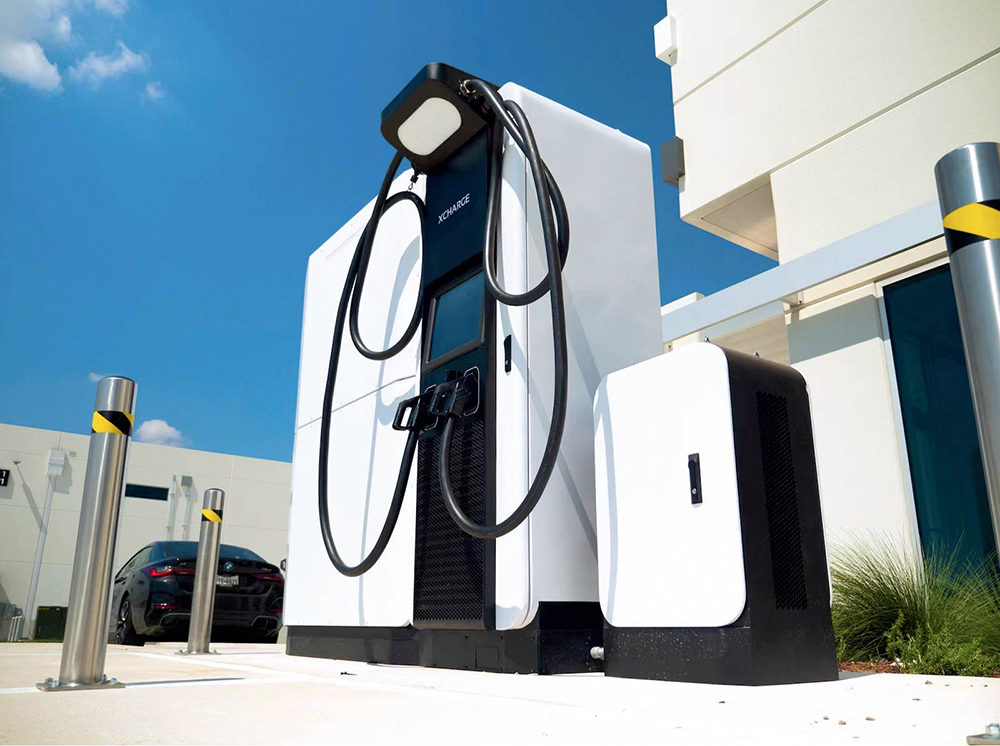
Charged: Tell me more about DC-to-AC conversion.
Alex Urist: Coming in from the grid, it’s AC. An energy storage solution is a DC system. You’re going AC to DC, and there is an efficiency loss associated with that. It works, but you should be prepared to lose some of the energy that you’re taking off the grid and paying for. A battery-integrated system has AC-DC bidirectional modules. The power is coming into the system via an AC-DC bidirectional module, and then any communication between the battery and the charging ports is generally through a DC-DC module.
If nobody uses the energy, there’s still ancillary grid services that can be taken advantage of, being able to put energy back into the grid.
It is similar to what you would find on an ADS-TEC or a FreeWire battery-buffered solution. However, those are not bidirectional modules. The FreeWire system can be input on split phase. ADS-TEC is still 480 three-phase. Everybody has their own niche that they fit into, but we like to think that a battery-integrated solution offers a little bit more flexibility in terms of what you can earn from an ROI perspective. If nobody uses the energy, there’s still ancillary grid services that can be taken advantage of, being able to put energy back into the grid.
Choosing the right charger
Charged: You have three different charger models. How do they differ?
Alex Urist: The Net Zero Series [NZSis the only product with a battery integrated into it. The other two units are standalone DC fast chargers. There are three different output ranges for our units in different install applications. The standalone DC fast charger, the C6, is a platform we’ve had since about 2016. It has been deployed globally across 25 different countries. For the North American market, we modified the C6 to run on 208-volt three-phase to offer more flexibility in terms of install applications. With that, we’re able to put that charger in a lot more environments that you generally wouldn’t be able to put a DC fast charger into. Think about multifamily dwellings or hotels. Places you generally look to put in four Level 2 chargers, you can now put in one DC fast charger. Revenue opportunity is higher, your cycle count is higher, and the general utility to the public is also higher.
What we do see though, is that there are demand charges from the utility if there’s a sudden influx of usage on the charger and it’s not a steady rate. That’s why battery-integrated solutions became a priority. The output of our first product line, the C6, is in the 50- to 150-kilowatt range. Then the NZS fits in that 200- to 300-kilowatt range. When we look at gen three, we have the C7, which we’ll be releasing in the US soon, which is in the 400-kilowatt range. That’s really designed for a charge point operator, a big public charging network operator that needs a lot of power.
It’s important to point out that ultra-high output is not necessary for everybody. Your 400-kilowatt chargers matter for Interstate charging sites, they matter for heavy-duty EVs, but we don’t need them everywhere. That’s why our product mix plays into what the infrastructure constraints are in the US. We have a solution for every step along the way, but we like to understand what a customer is trying to solve with their charging infrastructure and how can we achieve that with our hardware, as opposed to, “Here’s the biggest and baddest charger out there, go and get that bad boy in the ground now.” That’s not how we operate.
Charged: One thing I like about your web site is that you have a table that shows the charging times for some selected EV models, because this is something I see all the time from EVSE manufacturers. They say, “It can charge an EV in X minutes.” But there are so many variables that a figure like that is practically meaningless.
Alex Urist: There’s so much that goes into estimating charging times. There’s the state of charge you’re coming into the charger with, whether the battery’s been preconditioned, even what the temperature is and how long you’ve driven that day. If we look at charging data, for an output of 300 kilowatts for example, you’re getting that for the first minute or three minutes of your charge cycle and then you’re dropping. You get a lower amount for another six to eight minutes and then you’re dropping again to something around the range of 50, maybe 40 kilowatts.
Everybody wants the biggest and baddest toy in town, but two to three minutes, that’s just a couple more minutes in line at the McDonald’s where you stop to charge, and it’s only practical to stop at those types of locations if the local infrastructure can support the charging rate. Ultimately, that’s not a reality if we want every charger on 480 three-phase, because you’re going to have to upgrade the utility interconnect. Whereas if you had a 208-volt solution, you can drop one or two chargers in an area. If you have a battery-integrated solution, you can drop one or two in an area and it starts to become a meaningful revenue stream locally as opposed to this idea of needing to build the gas station of tomorrow.
Integrating with solar
Charged: Obviously, to get the most out of the battery integration, and take the utility out of the equation, we need onsite generation. Tell us about that.
Alex Urist: The NZS is capable of direct integration with photovoltaics in our generation-three unit, which is slated to be ready for customers in July of next year.
Charged: Integrating directly with photovoltaics avoids a DC-AC conversion?
Alex Urist: Bingo. It’s a DC-coupled solution. You don’t have to go through a separate DC-AC-DC solution. That’s how it would generally work if you were, say, integrating a battery-buffered solution with photovoltaics right now. That’s another benefit of the battery-integrated solution: it’s meant to be the central hub for everything you’re completing as a grid service. It’s not like the battery on your phone that can only function with your phone. It’s supposed to provide some ancillary service or ancillary charging ability.
Charged: Is there a formula for how much generation you would need for a particular charging hub? For example, let’s say I’m going to have X number of EVs per day charging at this site. Can you say, “Then you need Y square feet of photovoltaics?”
Alex Urist: There’s partners that we would work with to help run through the equations on that. It’s dependent on a lot of different factors. There are restrictions on how large of a system you can effectively integrate into the NZS. Also, it’s going to be very hard to get a photovoltaic array that’s going to make up the entire energy that you need to power a charging hub. The best way to think about integration of photovoltaics is to cut the dependence on energy from the grid. Effectively, it’s like ancillary peak shaving as well. You’re able to put more energy into the car that’s not coming from the grid and you can set your eco mode accordingly, which is all controllable via the OCPP backend or via the software that we provide with the units.
The additional value is that you can feasibly take in lower-cost energy overnight, then sell that energy back into the grid during peak hours, or use that to charge vehicles so you’re playing better off of your arbitrage. It is all algorithmically controlled via the backend and how you set your limits on when you want your charge and discharge times.
Different sites, different charging scenarios
Charged: Can you tell us a little bit about how the architecture differs for different kinds of charging sites? For example, a public charging site versus a bus depot versus a fleet of trucks?
Alex Urist: In any circumstance, it’s important to look at the infrastructure constraints on site to begin with, as opposed to trying to think about creating a solution for a given property or a given use case. From a public charging perspective, having the battery-integrated sites allows you to pack more charging assets in a given location on less energy. At 80 amps of 480 three-phase, you can get up to 194 kilowatts output on the current iteration of the Net Zero Series. That will be increasing in the next iteration.
You’re generally looking at a 200- or a 300-amp breaker on a 75- to 150-kilowatt DC fast charger. You’re going to need a smaller breaker size with the battery-integrated assets. There’s some really good studies on what Tesla has done for their load balancing and load management. It’s like 250 amps on the breaker that go in and that allows them to effectively control their demand chargers throughout the day that way.
A battery allows you to control your demand charges, which helps mitigate your overall operational costs, making more money on an Interstate location. When you take that same type of rationale to a bus depot, a depot is going to have heavy spikes of energy usage, given that it’s off-duty-cycle times. Generally, the buses are not going in and out all day—there’s a period where they’re charging on one cycle and then they flip, and the next cycle comes in. It’s generally a longer charge period.
With the Net Zero Series, or our standalone DC fast chargers, you can set a longer charge period. You can set load balancing across the entire site to say, “We only want to consume X amount of electricity,” and that’ll balance across all of the assets. Again, it depends on the constraints of the site, and what you’re trying to accomplish with the infrastructure you have. If you need more energy, put an NZS in because you can connect on 480 and it’s already there, but depending on where you are in the process of your electrification journey, it might make more sense to put a couple 208 assets in there—that can be a bridge solution.
For a fleet of trucks, a 208-volt solution is very interesting. Effectively, it’s like a Level 2 charger for a heavy-duty truck. If you’re looking at municipal fleets that are using heavy-duty trucks, battery-integrated assets are great because you can provide power back to the building. That’s one big benefit, particularly for government sites, that you can provide that as emergency energy storage.
There are a lot of benefits to having battery-integrated solutions, but it really is dependent on what infrastructure constraints you’re given. There’s not going to be a carbon copy best layout for every single property around America. That’s just not how our grid is designed. It’s finding the best hardware for the constraints that you’re given. That’s what we offer in the flexibility of our product line.
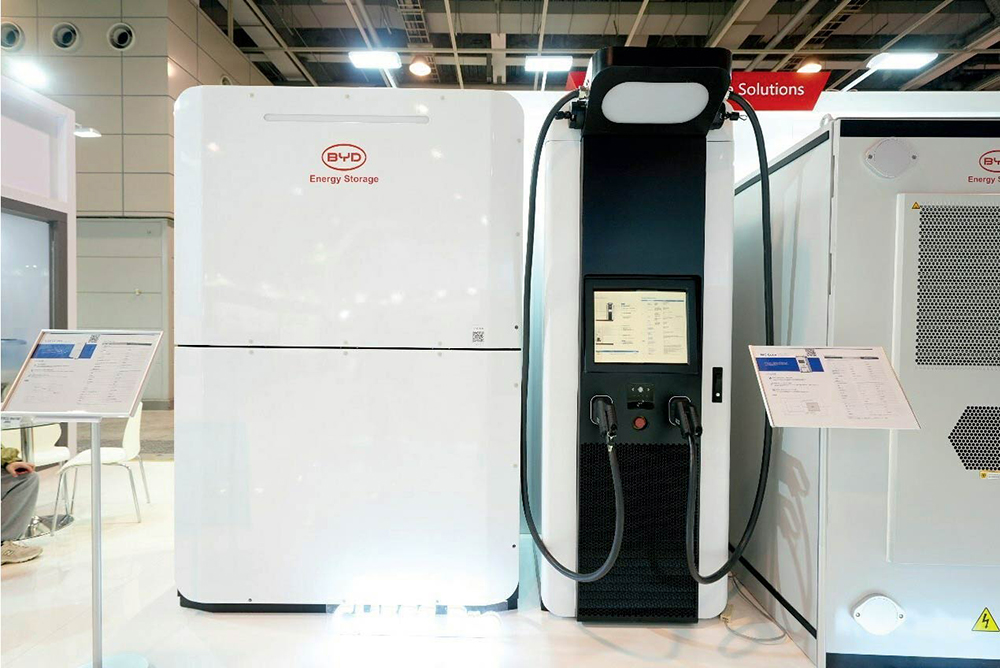
Charged: What about a totally off-grid location? How would the architecture there differ from a more typical grid-connected charging hub?
Alex Urist: You’d be eliminating any of the interconnection from the grid to the unit, but what you would still be looking at with the bidirectionality is providing an AC load back to a building, which the NZS is capable of. Powering a building from the battery. But effectively, the way that you’d be looking at it is DC-coupled photovoltaic solution pulling in solar, pulling it into the DC input, which is separate off of the charger itself. Then you’d be able to pull in solar, ideally running the asset off of that. You would be limited in the total amount you can charge per day. The battery’s 233 kilowatt-hours, so you can generally charge about four to six cars per day off of that.
Charged: Can you just add more battery storage to serve more vehicles in that case?
Alex Urist: Yep. You can add another pack for up to 466 kilowatt-hours in the current iteration of the NZS. Effectively, you could stack more assets in a given property, but they won’t run in series necessarily. You would have to have the photovoltaic arrays connected to those assets independently.
Loosening the utility bottleneck
Charged: That leads neatly into my next question, which is about utility interconnects. Say a fleet customer wants to deploy 50 EVs, but they don’t have enough power, and the utility tells them it’s going to take two or three years to upgrade the connection. I know you’ll say to talk to the utility early in the planning stages, but what other advice would you give as far as mitigating that bottleneck?
Alex Urist: Obviously, it is talking to the utility company early in the process and that’s what I’m always going to say. I think another thing is to be creative around the solutions that you can deploy and don’t be set on something as the only solution. We will only see increasing problems with timelines on utility service upgrades with demand increasing, particularly as you see NEVI projects coming online.
The other thing that’s important is understanding how much capacity you have available on site to begin with. There is a solution to be made. If you have limited power available on site, you just need to know how much that is and what your duty cycle is, how many cars are you trying to charge, what’s your scaling plan.
Electricity is super-complicated. I’ve talked with a ton of folks in the utility industry and I cannot even begin to imagine trying to plan out some of the stuff that they have to deal with.
There’s really nothing we can do about the utility companies and how long they’re going to take on upgrades until there’s a significant increase in the workforce, and frankly, the bureaucratic nature of utility companies to make that happen. Electricity is super-complicated. I’ve talked with a ton of folks in the utility industry and I cannot even begin to imagine trying to plan out some of the stuff that they have to deal with. I wish it was as easy as just plugging in a charger to the grid, but it doesn’t work that way, unfortunately.
Different regions, different challenges
Charged: You sell in several different regions. What can you tell me about the difference between those markets? How would your pitch to a customer differ if they were in a US state or maybe different regions of the US versus in Europe?
Alex Urist: The US pitch versus Europe versus the Asia-Pacific region would be entirely different. I mean, just look at voltage in general. Any time you’re putting in a DC fast charger in the US, you’re going to need to get the utility involved or some step-up infrastructure involved, something to get you to 480-volt three-phase. However 480 three-phase in Europe is very commonly available. It’s not as much of a difficulty to get you to where you need to go, given that everything is based off of 240.
Obviously, looking at the difference of 120 or 240, US versus Europe and the rest of the world, there’s differences. I think they face much more of a constrained grid market in Europe. But one thing that’s quite interesting is that you see a lot of chargers deployed in Europe that are not like our massive 400-kilowatt chargers. They’re starting to come out more, but a lot of that early infrastructure is actually within the 60- to 120-kilowatt range, which is quite fascinating when our policy and all the regulation that’s been released in the US is really predicated around that 150-kilowatt minimum and our European counterparts, who are further along in the electrification journey, are not mandating those output requirements. Both APAC and Europe, we don’t see as high an output requirement. Hence, the C7 came about.
Also, in the European market, the customer type varies greatly from the US. There’s definitely a lot more emphasis in the US on the independent business owner and the individual being able to reap the benefits of public incentives to get charging infrastructure in. In Europe, a lot of the customers are utility companies or charge point operators. We have a lot less of this “go and get the public incentive to get your charger at your property” type of situation going on there, so it centralizes the purchasing patterns a little bit more.
Charged: Are you saying that in Europe, for a given project, there are likely to be fewer organizations involved? I know in the US, it seems like a lot of infrastructure installations, there could be 10 different companies and government agencies involved by the time it’s done.
Alex Urist: Yeah, it definitely feels consolidated more. Most of the time in Europe, you’re working with a public agency who’s going through an RFP process or something of the like. In the US, there are a lot more private market players. You have the site host, the utility company, your EDC engineering, design and construction partner. Sometimes there might be a turnkey partner involved who’s actually the customer contact, then you have the manufacturer, and your OCPP backend. Everybody wants to have their piece of the pie when it comes to developing projects in the US. Whether that makes projects more efficient or less efficient, time will tell.
Charged: Just to clarify, what you need as an input for your chargers is a 480-volt three-phase connection, and that is the norm in Europe, but in the US, that usually requires some kind of a step-up transformer, correct?
Alex Urist: Generally, you need a service upgrade in the US every time you’re dealing with 480 three-phase, and that’s the norm for DC fast charging infrastructure that’s being deployed in the US. What we’ve created is the ability to install on 208-volt single-phase, which is available at about 95% of commercial locations across the US.
Charged: We hear a lot about having to have a service upgrade, but does that always mean more power, or might it just be a case of needing 480 volts?
Alex Urist: It’s generally both. A service upgrade will generally be pulling a new line of service from the substation, to a transformer that then puts that into 480 three-phase for you. If a CPO comes into a property, they will generally go and get a new line of service put in. A service upgrade will also generally involve a capacity increase where you’re increasing the total capacity of energy that you can deliver to a site, for example going from 1,000 amps of service to 1,500 amps of service, and you’re often going to need to do a panel upgrade—but the panel upgrade is definitely cheaper than having to put in a transformer and do a service upgrade.
Charged: Are utility interconnect bottlenecks more of an issue in certain parts of the US than others? Is that a regional thing?
Alex Urist: Definitely. I mean, it’s a problem everywhere. Anywhere you’re thinking of more congestion, that is certainly an issue. The service upgrades also come in and where you…have more people trying to do more activity on the grid, that congestion increases those upgrade times as well.
Charged: Are areas with higher population density likely to have more problems?
Alex Urist: Correct. But then the other side of that is that rural areas, where there’s not a demand, also have a long period. Because the substation might be a ways away and they previously had no reason to have any 480 V service on site. Just getting that pulled out there can be quite a challenge.
Charged: A different set of problems depending on where you are.
Alex Urist: Yes, different set of opportunities.
Turning to Tesla
Charged: What about this rush to adopt the Tesla connectors? We all know the Superchargers are more reliable, but I’m a little skeptical that is still going to be the case when everybody’s hooking up to it.
Alex Urist: I would definitely echo some of your concerns. I think there’s going to be some kinks to shake out for auto manufacturers and for Tesla on interoperability. Adopting the NACS cable is not a fix-all for charging reliability per se. I think a lot of that issue comes with the interoperability questions. A lot of it comes with payment solutions and integration.
At XCharge we’ve been manufacturing NACS cables and deploying them on our chargers since March. Our rationale is that 70% of EVs on the road are Teslas, so we would be foolish not to service them to begin with. I think we’re going to see a lot wider availability of charging options generally. Sure, the Supercharger will be a preferred place for Tesla drivers because it’s their network, but I think there are going to be some issues early on with opening up that network that are going to turn off some other drivers. Having solutions on other networks and other hardware is important too. We’ve definitely stood by.
It’s not that the technology is necessarily better, it’s that the Tesla charging network has operated more efficiently.
Technologically, I don’t think it’s more efficient necessarily. It’s not that the technology is necessarily better, it’s that the Tesla charging network has operated more efficiently, but the Tesla charging network has had no payment terminals on their devices and they haven’t had to deal with other manufacturers with different voltage architecture in their batteries. The Tesla network is only rated up to a 650-volt architecture, so when you get into the 800-volt architecture of the Hyundais and the Mercedes, you might have a little bit of a diminished charge rate in those vehicles or potentially spiking issues going on.
Going bi
Charged: Everybody I talk to, I ask about bidirectional charging, and I get different answers. Some people say it’s a huge game-changer, but some, mostly on the utility side, say they think it has limited application. But one thing everyone seems to agree on is that, right now, vehicle-to-grid is a pilot-stage technology.
Alex Urist: I think it’s still within the pilot phase. There are distinct applications in the school bus space, fleets, and then there’s something to be said about residential play as well. I still have questions. What central remuneration platform is there? If I’m providing my energy, how does that play out on the virtual power plant side of things? Who’s the broker of that energy buyback? Are the utility companies directly purchasing it from, say, a residential user or from a corporate user? There are a lot of logistical questions that go into the payback process, aside from any of the technological components.
I don’t think it’s going to be as clear-cut as people think, like you have all the cars plugged into the grid and this is how much energy you have to pull on. I think there’s a lot of demand signals that are going to have to come into play for the remuneration to even happen, and then how much remuneration are we talking about? Is it cents on the dollar, or is there actually a meaningful payback? It’s really hard to judge at this current stage. It still needs to go through more pilots.
Is it a virtual power plant play? Is it more akin to a Tesla Powerwall type of play, where you have solar that’s generating into the battery and then Tesla can say, “Hey, we’re going to sell this back to the Texas grid because we have a virtual power plant agreement and then we’re going to pay you out a fraction of what we’re able to get?” That seems like that would be the best way to run it, but then that’s one company that’s aggregating the assets across that. That’s what we would say is the play for our battery-integrated assets as a stable asset. There’s one identifying authority that’s trading the energy back.
But when you bring in individual private landowners, there’s got to be an aggregating authority that’s going to handle the payback, but then how much of a margin are they taking? Is there a way to opt into other services? Are you stuck with, say, ChargePoint’s V2G program because you put in a ChargePoint charger? What’s the overall process? Do they have an interconnect agreement with a utility? I think that’s just where a lot of the questions are being shaken out.
Charged: But your hardware is technically capable of V2G any time that everybody else is ready to get on with it?
Alex Urist: Yep, exactly. It’s effectively a software enablement at this point.
This article first appeared in Issue 66: October-December 2023 – Subscribe now.
from Charged EVs https://ift.tt/gvTjeO8