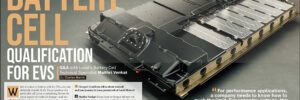
Q&A with Lucid’s Battery Cell Technical Specialist Maithri Venkat.
When it comes to battery cells for EVs, one size definitely doesn’t fit all. The properties of a particular cell act as constraining factors for every aspect of a vehicle’s design—and not only for vehicle performance parameters such as range and power, but for the development of manufacturing processes as well.
Lucid Motors has a team of battery specialists that collaborates closely with cell suppliers to evaluate and test battery cells at every step from vehicle design through mass production. Charged spoke with Lucid Battery Cell Technical Specialist Maithri Venkat about how cell evaluation works, and how OEMs and cell suppliers can work together to improve the process.
Charged: Could you tell us about yourself and your journey to your present role at Lucid Motors?
Maithri Venkat: I have been working in lithium-ion cell development for automotive applications for the past eight years. In my current role as a Technical Specialist at Lucid, I lead next-generation cell selection, qualification and key supplier partnerships for the Gravity SUV. I have worked on multiple aspects of battery development, from cell material evaluation to design tradeoff assessments to performance optimization and new product introduction.
Previously, I worked at XALT Energy, where I benchmarked cell designs and sub-components for high-energy cells for transportation and marine requirements. I have also collaborated with top-tier OEMs and national labs for 12 V Li-ion start/stop battery development.
For performance applications, a company needs to know how to push the limit. For economy options, the cells are the biggest cost driver in the vehicle.
Charged: Can you elaborate on why battery cell development is so important for electric vehicles?
Maithri Venkat: As automakers commit to electrification, the market requirements are becoming more diverse for different types of EV products—longer range, faster charging, sports car-level performance numbers and long life. The battery cell impacts all of these.
How one designs, tunes and manufactures the battery cells also impacts their effectiveness, performance and cost. For performance applications, a company needs to know how to push the limit. For economy options, the cells are the biggest cost driver in the vehicle.
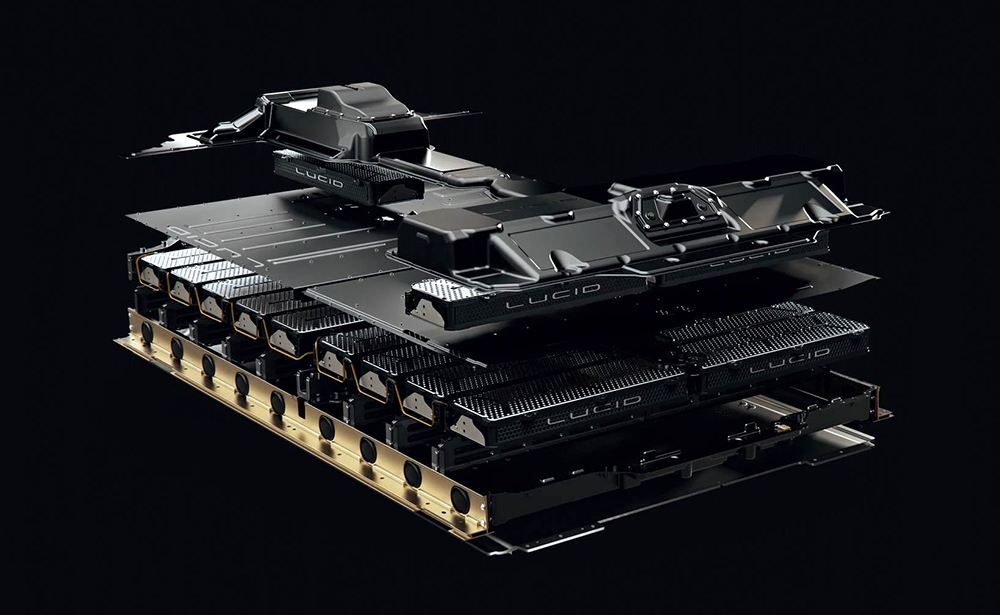
Battery cell development is critical at every step of the development of a vehicle, but especially at the beginning conceptual design phase, where the vehicle-level product definitions are translated into cell-level technical specifications. Technical assessments and commercial requirements are evaluated by EV manufacturers during cell selection and qualification. Once the cell design is finalized, it is fine-tuned further for energy efficiency, fast charge capability, power capability and lifetime requirements, prior to deployment in packs and vehicles. This early stage of cell development paves the way for best-in-class technological advancements.
Once the cell design is finalized, it is fine-tuned further for energy efficiency, fast charge capability, power capability and lifetime requirements, prior to deployment in packs and vehicles.
Charged: Can you walk us through the preliminary stages of the cell qualification process? What do we need to consider even before going into cell selection?
Maithri Venkat: Cell development for automotive applications needs to happen years in advance. This ensures that we have enough time to iterate through cell design changes. In general, cell development begins with the creation of vehicle-level performance targets.
For example, a vehicle’s intended usable range is a key metric in the qualification process. Target range requirements are defined based on an array of research, including marketing surveys and consumer feedback. With those established, we can apply technical constraints such as vehicle and powertrain efficiency, pack sizing and vehicle weight class, to transform range into usable energy per cell.
Prior to defining battery pack constraints, we need to analyze and balance performance, durability and cost. This requires in-depth collaboration among cell engineering, systems, vehicle integration, efficiency, software and marketing teams.
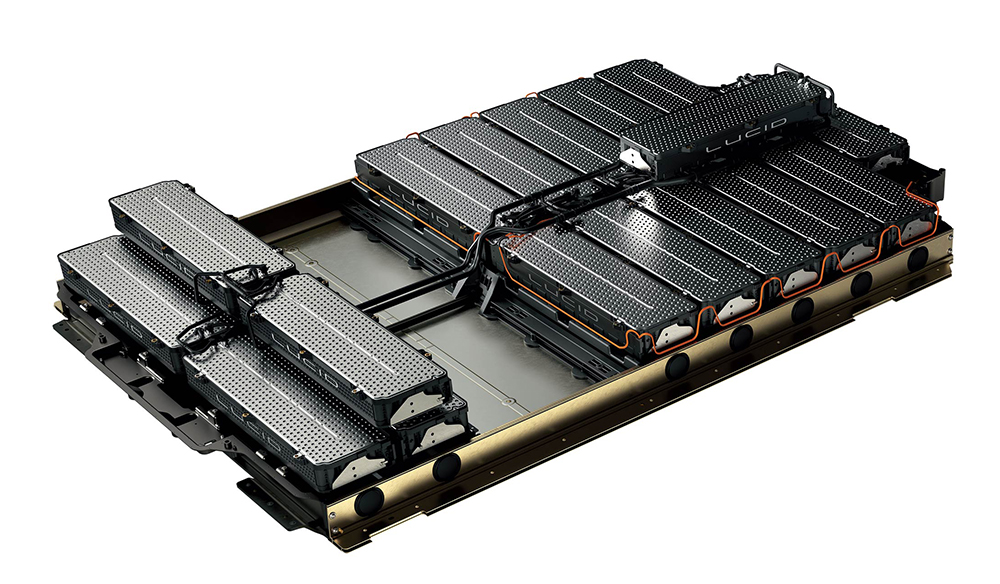
Following vehicle definitions and alignment on cell performance objectives, specification sheets are sent over to cell suppliers. This creates an iterative feedback loop between OEM and cell supplier, and triggers gap analysis between requirements and technology readiness.
Identifying these performance gaps and quantitatively understanding the limitations of specific cell chemistries helps with future cell development. For instance, for high-energy cell design, material-level changes such as silicon for anodes, high-nickel cathodes, or solid-state chemistries could be considered. This would enable technological advancements and define clear actionable objectives to bridge the differences between current-generation and next-generation technologies.
Charged: You mentioned the need to translate vehicle-level requirements into cell-level targets. How do we accomplish that?
Maithri Venkat: Once the vehicle conceptual design has been finalized, requirements trickle down to pack and module levels before getting down to cell-level definitions.
Every high-level target can be tied to an individual parameter of the battery cell. For example, pack size, efficiency and range can be defined as energy requirements for the cell. 20-80% SoC (state of charge) charging times can be translated to fast charge capability of the cell. Product warranty requirements [can be translated to] lifetime performance of the cell, and so on. Form factor selection can be dependent on pack sizing strategies, thermal management systems for cooling, ease of manufacturability, and even ease of repair.
Cell peak or continuous power targets are related to the 0-60 mph vehicle performance requirements and towing capacity. Detailed power capability assessment is helpful to provide the necessary performance when you want to—for example—tow your jet ski to Lake Tahoe. Or, on the way home, roll down a hill and regeneratively brake at freezing ambient temperatures for over an hour.
Charged: What are the steps a company takes to qualify a new cell supplier?
Maithri Venkat: We evaluate cell suppliers for several top priorities, including safety, quality, cost, performance, volumes, technology roadmap and technology capabilities.
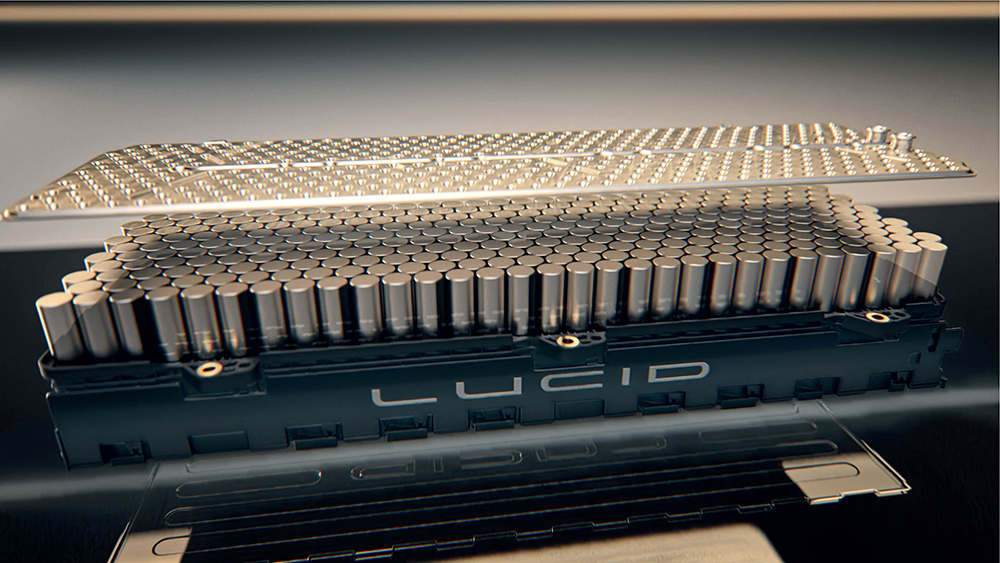
For example, when it comes to cell quality inspection, production batch lot-to-lot variation must be within the defined engineering specifications, and process variations should be within Six Sigma control limits. In the initial stages, routine cosmetic and electrochemical inspections need to be conducted on available samples. Cell dimensional properties and appearance of dents, rust or scratches should be thoroughly assessed to understand manufacturing process capability. For electrochemical inspection, it would also be advantageous to conduct regular testing for performance characteristics like energy and resistance. If cell-to-cell energy variations exceed certain threshold values, there are risks in terms of battery pack imbalances.
Another aspect to consider is the supplier timeline. Auto manufacturers need to ensure that their development timeline aligns with the cell manufacturer’s milestones for concept, design and process validation stages. Cell mass production should be well in advance of the product introduction timeline.
Charged: Once a cell design is finalized, what are the next steps to be considered? What types of tests are appropriate for each developmental phase?
Maithri Venkat: Following cell design finalization, multiple workstreams happen in parallel as part of the product development cycle. I am currently leading and facilitating these efforts for Lucid’s Gravity SUV platform. These include fast charge, durability, process capability, cell parameterization for software controls, and testing for state of health/thermal modeling. Here are some examples of that process flow at Lucid:
Parameter measurements: Once representative cells are available from the manufacturer, an extensive suite of cell testing and data processing is kicked off for Equivalent Circuit Modeling (ECM) development. The cell parameter datasets obtained from testing are essential for accurate state of charge (SoC) and state of health (SoH) estimation.
Using actual cell testing data, we can get insights into setting up control limits, and trace how the gaussian energy distributions would scale up at pack level when cells are distributed in series and parallel connections.
Variability studies: From the process capability side, it is essential to track cell-to-cell variability through design validation, process validation and final mass production phases. This helps vehicle systems modeling, integration and product teams gauge the estimated range and performance for the final product. It’s also important to characterize nominal capacity and energy distributions after analyzing representative drive profiles with discharge/regeneration pulses incorporated within testing intervals. Using actual cell testing data, we can get insights into setting up control limits, and trace how the gaussian energy distributions would scale up at pack level when cells are distributed in series and parallel connections.
Optimization: Miles charged per minute defines fast charge capabilities. Comprehensive testing is done at cell, module and pack levels to understand the failure modes and lithium plating thresholds over the cell lifetime. This facilitates the selection of fast charge profiles and helps push the performance boundaries.
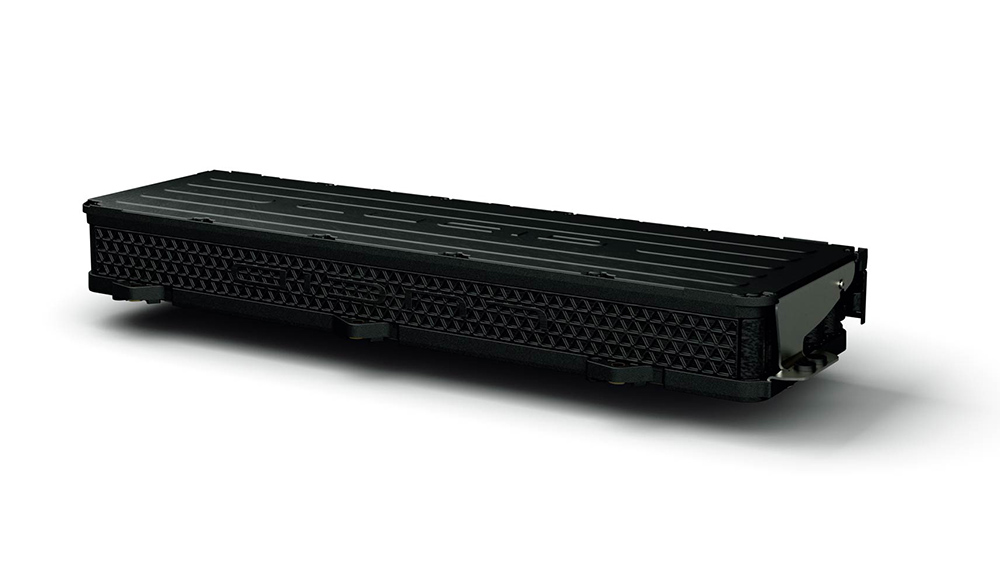
Modeling: State of health (SoH) for lithium-ion batteries needs to be predicted accurately for software controls and for prolonging cell usable lifetime. Physics-based cyclic and calendar aging capacity decay models are developed to capture loss of positive/negative electrode material and lithium inventory over battery usage.
Charged: What are some common misconceptions about defining cell specifications for automotive usage scenarios?
Maithri Venkat: Cell engineering specification sheets are extremely conservative in certain cases. As an example, laboratory cell cycling with 1C charge and 1C discharge could trigger unexpected degradation modes like lithium plating and gas generation. In the case of the Lucid Air Dream Range edition, the vehicle’s range is 520 miles at top of charge, and 1C discharge would mean depleting 520 miles in one hour. This is an impossible scenario in the real world, even if we assume the lowest efficiencies during discharge. Cells are far more capable when we conduct experiments under the range of conditions accessible to a customer. It is therefore important to consider that testing under the right conditions can help access more representative limits of performance boundaries. As an analogy, Olympic teams don’t pick their marathon runners based on their performance in a 100-meter dash!
Furthermore, certain supplier specification sheets are based on consumer electronics, for which energy estimations are calculated with extremely low constant-voltage cutoffs at the end of charging sessions, or cells are cycled continuously between zero and 100% state of charge. Users of EVs rarely charge to 100% and then drive down to zero. As a result, it doesn’t always make sense to perform testing and specification setting with such usage patterns.
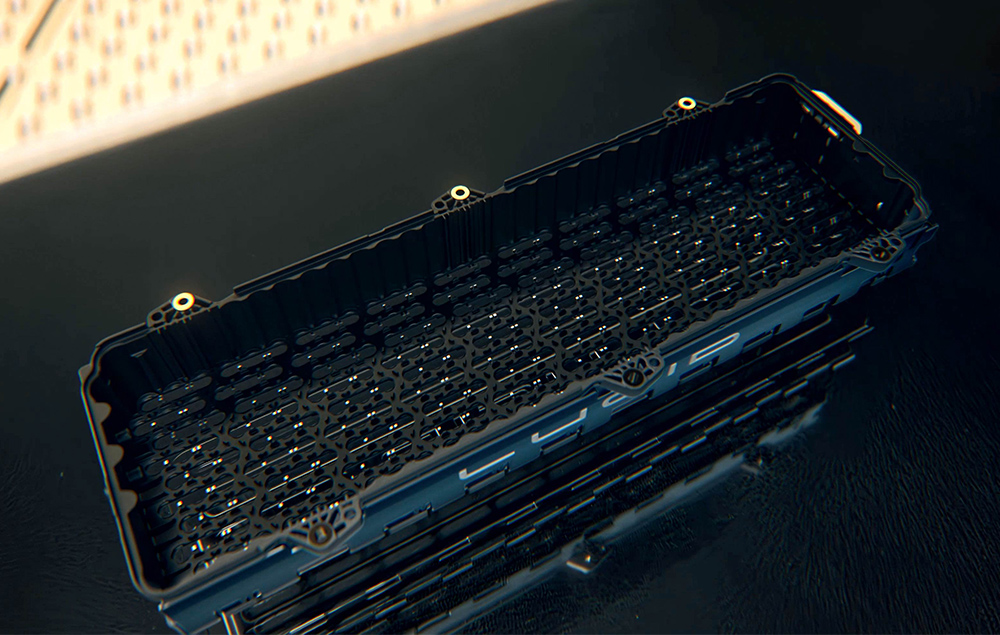
Charged: How can automotive companies help cell suppliers develop specifications?
Maithri Venkat: We should ensure that supplier specification sheets match automotive use cases. I acknowledge that it is challenging to specify an exact automotive use case. However, it would still be valuable to rewrite the specifications to conform more closely to what customers might experience.
At Lucid, battery data scientists use fleet telemetry data to understand realistic usage profiles. Fast charge performance boundaries are evaluated based on the preferred charger type, temperature regimes and state of charge (SoC) for session beginning and end. Automotive companies can teach cell suppliers a lot that may go back into their development processes and help them make a better product.
Therefore, it would be beneficial to have continuous communication between cell manufacturers and OEMs for incorporating consumer usage profiles in engineering specifications.
Lastly, it would be beneficial for automotive companies to drive specifications development. Eventually, this serves the best interests of both cell suppliers and OEMs.
Charged: You mentioned realistic profiles earlier. How do we incorporate real-world aging into laboratory testing? Is there a way to strike a balance between using aggressive aging vs realistic aging profiles for cell evaluations?
Maithri Venkat: It is of paramount importance to understand the tradeoffs associated with using aggressive vs realistic aging profiles prior to determining the design of experiments for laboratory cell assessments. Testing methods involving slower charge/discharge, reduced depth of discharge and average temperatures can be ideal for replicating typical EV usage. Under these conditions, lithium-ion batteries would experience the degradation mechanisms such as solid electrolyte interphase (SEI) growth that are observed in real-world driving. However, this would also imply much longer test timelines to obtain capacity loss and resistance growth data.
On the other hand, using accelerated aging could result in lithium plating on the anode due to diffusion limitations or gas generation from electrolyte solvent reduction reactions. While the testing time is reduced, the failure modes are not representative or even achievable for these corner cases.
Ideally, one needs to choose intermediate charge/discharge rates with rest steps incorporated between cycles for effective performance scale-up.
Charged: What are the cell sample quantities necessary for each developmental phase?
Maithri Venkat: Cell sample size required will increase through the developmental phases. For supplier evaluation and cell design screening, it could be sufficient to start with hundreds of early R&D sample cells. However, once the design is confirmed, performance optimization and durability testing would require thousands of cell samples. After this, we get into module and pack testing. The cell quantity required for this is 10 times more compared to the previous phase. Subsequently, the final vehicle testing phase would require over 100 times more from the mass production line compared to initial R&D evaluations. It is important to remember that larger quantities for cell allocations need to be available far in advance of the start of vehicle production.
Charged: Why are representative battery packs required for vehicle testing months in advance of the start of production?
Maithri Venkat: This is related to the type of vehicle validation and regulatory tests being conducted. Having an early start to validation helps offset longer lead times associated with testing and data procurement. Examples include vehicle fleet deployment, hot/cold weather climate testing, homologation and SoC/SoH software algorithm validation. Electric vehicles need to go through mileage accumulation and standardized durability testing to ensure consistent long-term performance, reliability and warranty assurance.
Charged: Eventually, the goal is to get cells into cars. What would be some of the key tasks that we need to track while moving towards manufacturing scale-up during EV production?
Maithri Venkat: Even after completing performance optimization and reliability assessments, we still need to be mindful of new product introduction in the factory. As we move towards production ramp-up, we need to consider cell integration into modules and packs at the manufacturing stage. Each cell type needs to have a distinct manufacturing part number, equipment settings, and even data handling. Even mundane changes like barcode placement on a cell box can dramatically impact yield if process controls are not thoroughly optimized.
Another example is the implementation of fully automated in-line inspection methods for checking key cell characteristics. These high-speed measurements, along with mid-process and end-of-line measurements, help us ensure that the processes involved in building modules and packs have not impacted the integrity or performance of our cells.
Charged: What about the overall timing? How much time do we typically need to qualify a cell for automotive usage?
Maithri Venkat: Cell development for automotive applications happens years in advance. Since every cell has unique characteristics, it is essential to conduct detailed testing throughout the qualification stages to probe into cell degradation mechanisms and evaluate performance thresholds.
We would need to evaluate the development timeline on an individual basis. The time required would be dependent on requirements, technology readiness, cell chemistry, manufacturing feasibility, and the intended EV application and market. Speaking generally, it is a few years.
It is also possible that even a mundane process change from a cell manufacturer could have unintended yet severe impacts downstream for an automotive maker. Therefore, every single change to a cell needs to be scrutinized.
Let’s also consider a scenario in which the cell chemistry is frozen, and there is a change with respect to a minor process during manufacturing. While this might create a significant improvement in yield, the team still needs to evaluate if it has an impact on performance or safety. For this example, it is possible that an entire re-qualification of the cell is not required, and the change can be quickly approved. However, it is also possible that even a mundane process change from a cell manufacturer could have unintended yet severe impacts downstream for an automotive maker. Therefore, every single change to a cell needs to be scrutinized. I want to highlight that every cell is unique. Qualification strategies and developmental timelines need to be evaluated on a case-by-case basis. Battery cells can be one of the most critical path items in your EV development.
This article first appeared in Issue 66: October-December 2023 – Subscribe now.
from Charged EVs https://ift.tt/woML84W
No comments:
Post a Comment