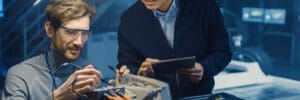
As electrification takes hold in all the legacy automakers, the topic of upgrading existing powertrain test facilities is a high priority. Whether it is converting traditional Internal Combustion Engine testbeds to support E-Powertrains or upgrading older battery lab cyclers to support higher voltages and powers, fitting in new test equipment, and supporting the new energy demand, is a tremendous challenge.
To achieve the upgrades needed to fulfill the testing requirements for the E-Powertrains of today, and tomorrow, three things must be considered:
- Available power
- Available space
- Available budget
These are probably no surprise to anybody that has been challenged with this task, but the traditional approach to solve this problem might not be achieving the best possible solution. Here’s why.
The traditional approach is to:
- Define the test cell upgrade need (i.e. add a battery emulator to a dyno testbed)
- Generate the equipment specification (i.e. 1200VDC, 330kW, 600A)
- Generate a RFQ (Request For Quote)
- Send the RFQ out to the top 10-20 suppliers
- After several rounds of clarifications and negotiations, pick the best one and proceed with the upgrade.
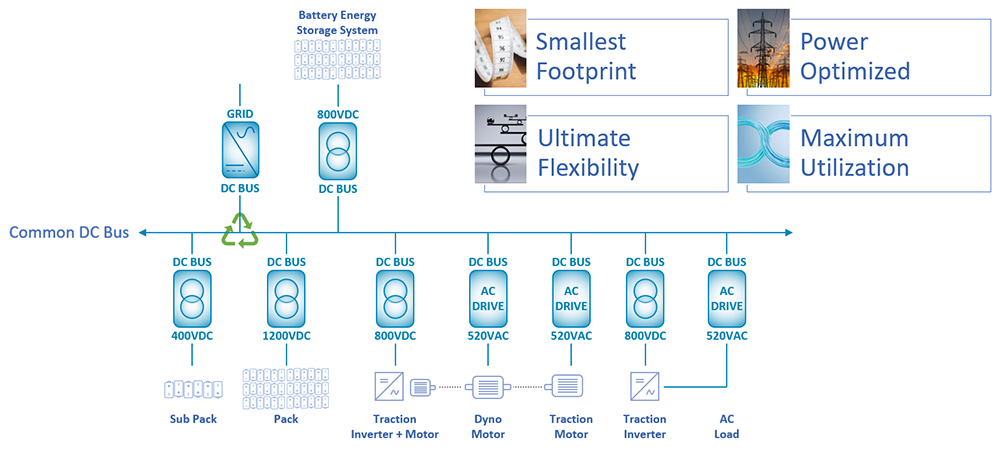
When this is then done with the 3 constraints listed above and with a myopic view of this single piece of equipment, a solution can be found, but it is not optimized from a facility or lab perspective. All of these individual systems added to the facility need floorspace and power, which are quite significant.
With the advances in power electronics with technologies like Silicon Carbide, options for energy management inside the equipment when combining AC and DC solutions into a single system offer solutions with reduced footprint and energy needs. SiC based resonant converters incorporated inside battery cyclers can offer true multi-channel battery testing with a single grid connection. Both of these benefits are enhanced even further when true energy needs are honestly considered. However, this requires a non-traditional approach to the upgrade process. Additional possibilities of adding Battery Energy Storage Systems (BESS) and renewable energy generation to the test systems for energy management can even allow Net Zero operation.
Unico has the building blocks needed for optimized lab solutions which can combine AC and DC applications into single systems which can recirculate energy to reduce the load on the facility as well as the number of new, high-power runs that need to be added . These systems also have a reduced footprint and cost which can utilize a combination of IGBT and SiC technologies as necessary to reduce costs for applications that don’t require the benefits of SiC power modules. The same systems can be multi-configurable to allow flexibility to test multiple powertrain configurations with a single system maximizing the utilization of the purchased power. Standard and custom solutions with switching frequencies up to 100kHz, parallel and serial DC operation for multi-megawatt powers and voltages of 1500VDC or more.
Unico has the perfect solutions for lab upgrades including:
- ICE dyno testbed to E-Motor testbed
- ICE powertrain to E-Powertrain
- 400VDC battery cycling to 1200VDC+ battery cycling
- 1-channel battery cycling to 2, 4, 6, or 8 channel battery cycling
- EOL multi-channel inverter testing with multiple active loads in a single system
from Charged EVs https://ift.tt/OFUCnMe
No comments:
Post a Comment