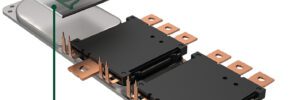
In the ever-evolving landscape of electronics manufacturing, innovation is the key to staying ahead. Indium Corporation®, a leading player in the industry, has once again demonstrated its commitment to advancement with the introduction of Indalloy®301 LT. This novel alloy technology is specifically designed for power module package-attach applications and enables lower processing temperatures in preform soldering.
Quest for Lower Processing Temperatures
One of the most exciting features of Indalloy®301 LT is its ability to facilitate lower processing temperatures. This is a game-changer, especially in power module applications, where thermal management is crucial. Package-attach soldering is a robust and reliable thermal management method, however the required processing temperatures for current state-of-the-art Pb-free alloys can cause catastrophic side effects such as mold delamination in the power module. By reducing processing temperatures, Indalloy®301 LT addresses this common challenge faced by manufacturers—how to achieve robust solder joints without subjecting the module package to excessive heat. The ability to reduce processing temperatures, and thereby energy consumption, is also of increasing importance as manufacturers strive to reduce their carbon footprints.
Meeting the Demands of Mission Profiles
The demands on power electronics applications, especially in areas like electric vehicle (EV) power module-cooler integration, are continually increasing. Indalloy®301 LT rises to the challenge by offering superior thermal and mechanical performance compared to traditional thermal interface materials. When leveraged with this new alloy technology, preform soldering can prevent issues like warpage, encapsulation breakdown, and delamination by reducing processing temperature.
Bismuth-Free Advantage
What sets Indalloy®301 LT apart is its bismuth-free composition. Traditional low-temperature alloys often contain bismuth which, while effective in lowering melting points, comes with its own set of challenges. Bismuth-containing alloys are known to compromise reliability over time, leading to thermal defects in modules. Indalloy®301 LT eliminates this issue, offering a reliable alternative that doesn’t sacrifice performance.
Configurations for Every Need
Indium Corporation understands the diverse requirements of the electronics industry. To cater to different preferences and applications, Indalloy®301 LT is available in various configurations, including InFORMS®, preforms, and ribbon. This versatility allows manufacturers to choose the format that best suits their production processes, ensuring seamless integration into existing workflows.
InFORMS® for Consistency and Strength
InFORMS® configurations of Indalloy®301 LT bring a new level of consistency to soldering processes. Consistent bondline thickness and improved strength enhance both thermal and mechanical reliability of solder joints. This is particularly significant in power module applications, where the performance of solder joints can directly impact the efficiency and longevity of electronic devices.
Enabling Pb-Free High-Reliability Alloy Technologies
Indalloy®301 LT doesn’t just stop at addressing thermal defects. Its lower processing temperatures open the door for complementary Pb-free high-reliability alloy technologies, such as Indalloy®276. This enables customers to utilize advanced alloys in power module die-attach, component-attach, or interconnects without the risk of re-melt and degraded performance.
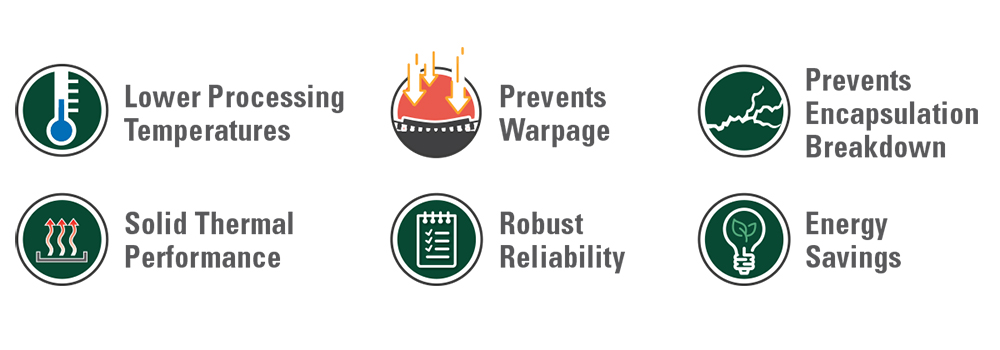
Key Features of Indalloy®301 LT
- Reduced Peak Reflow Temperatures: By reducing peak reflow temperatures 50°C compared to commonly used alloys in power electronics assembly, Indalloy®301 LT minimizes stress on the power module package.
- Prevention of Warpage and Delamination: Indalloy®301 LT prevents warpage and eliminates delamination in molded power module package-attach applications.
- Excellent Thermal and Electrical Conductivity: The alloy maintains excellent thermal and electrical conductivity, ensuring optimal performance in diverse electronic applications.
- Solid Reliability Performance: Indalloy®301 LT with its bismuth-free composition exhibits solid reliability performance within a wide temperature range (-40°C–125°C), meeting the stringent requirements of various mission profiles.
- Ability to Step-Solder with Pb-Free Alloys: The flexibility of Indalloy®301 LT allows for step soldering with Pb-free alloys, expanding the range of applications and design possibilities.
- Reduced Energy Consumption: Lower processing temperatures not only benefit the integrity of electronic components but also contribute to reduced energy consumption during manufacturing, aligning with sustainability goals.
- Available in Various Configurations: Whether in preforms, ribbon, or InFORMS®, Indalloy®301 LT provides flexibility and convenience for different manufacturing setups.
Conclusion
Indium Corporation’s new Indalloy®301 LT is a remarkable addition to the world of soldering technologies. Its bismuth-free composition, lower processing temperatures, and diverse configurations make it a versatile solution for power module package-attach applications. By addressing thermal defects without compromising reliability, Indalloy®301 LT opens up new possibilities for designers and manufacturers in the pursuit of enhanced thermal and mechanical performance in electronic devices. As the industry continues to evolve, innovations like Indalloy®301 LT are set to play a pivotal role in shaping the future of electronics manufacturing.
For more information about Indium Corporation’s high-reliability alloy products, visit www.indium.com/products/solders/solder-alloys/ or contact Joe Hertline at jhertline@indium.com.
from Charged EVs https://ift.tt/uqoy27E
No comments:
Post a Comment