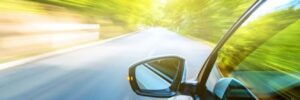
The future is electric. Indeed, the electrification of products, systems, and processes is happening at an accelerated pace in countless industrial and consumer settings. These changes are driven by advanced electronic technologies in lieu of conventional methods such as hydraulics and pneumatics.
Nowhere else is the acceleration of electrification more evident than in the transportation industry. The number of vehicles loaded with cutting-edge functionality and fully electric powertrains is growing at a record pace.
In addition to the rapid emergence of all-electric powertrains by replacing the long-serving internal combustion engine (ICE), the electric content on a typical vehicle has also grown significantly. Case in point, many critical systems that were previously mechanical are now using electronics to improve safety and reliability. Braking assist and steering (electronic power-assisted steering – EPAS) are just two examples. And more recently, solutions supporting Advanced Driver Assistance Systems (ADAS) are progressing rapidly through defined levels toward the holy grail of fully autonomous driving.
More Choice and Better Performance Equals Faster EV Adoption
In the last several years, the number of electric vehicles (EV) and hybrid electric vehicles (HEV) has increased globally, with predictions accounting for 20% of new car sales in 2025.
The number and diversity – from compact cars to large pick-up trucks – of different EV & HEV models available has risen significantly in the global market. In addition, evolving battery, power management, and regenerative systems are resulting in longer ranges on a single charge, bringing the travel distance possible between ‘refueling’ closer to those of gasoline-fueled vehicles. With the range of an EV increasing, range anxiety is decreasing the apprehension that has slowed adoption in the past. And, as the network of charging stations expands and rapid-charging becomes more prevalent, the ‘gap’ between the EV and ICE-powered vehicles will reduce further, with EVs potentially taking the lead.
Challenges to Electrifying Vehicles
Despite all of its promise, barriers remain to vehicle electrification. What challenges are automotive manufacturers facing to get their share of a market forecasted at USD236.3 billion, with a CAGR of 10.6%?
According to the recent “Electrification Innovation in Automotive” survey conducted by Molex and third-party research firm, Dimensional Research, concerns are real and present, with 92% of respondents indicating that their design teams are facing additional challenges as they work on supporting increase electrification.
Getting in the Zone
Consumers are demanding more than just a source of transportation from their vehicles. Making them safer, comfortable, convenient, and packed with infotainment functionality, is a priority for automakers. Today’s functionality can make contemporary vehicles feel like an extension of our working and living spaces. But a plethora of electronic systems and modules create considerable challenges in terms of the electrical architecture of a typical vehicle.
To meet consumer demands, the design of high-end vehicles can have over 100 electronic control units (ECUs). More ECUs in vehicles bring challenges in how to connect, package, and manage these systems that transport command-and-control specific functions that are vital to the vehicle. With incumbent architectures reaching limits of scalability, this is where zonal architecture comes in. By segmenting the vehicle into zones, each zone has assigned functionality and then passes information between the zones as necessary. Zonal architecture affords not only the overall volume of wiring to be optimized and reduced, but also the ECUs to be consolidated. In addition to gaining topology that is better suited to the increasing number of electronic systems in the vehicle, zonal architectures can result in a weight savings that translates into increased efficiency and improved range on each charge. Successful implementation of zonal architectures requires high data speed data connections that are flawless, robust, and can keep data flowing securely.
According to the survey referenced above, 84% of respondents agreed that adopting zonal architecture is the future and will help address concerns as traditional approaches reach their limits. Molex has many solutions that facilitates the transition from the existing traditional approach, through all the intermediate phases and ultimately a variety of exceptional industry leading flexible products to support a true zonal architecture.
Feeling the Heat
With the strong uptick in electronics being designed into vehicles – both ICE vehicles and EVs – comes the challenge of thermal management. What happens when an electronic device such as a computer or a mobile device gets too hot? It shuts down – not an option for a vehicle traveling down the road at highway speeds. So, how do you design for a vehicle that now has more than 100 ECUs and exponentially more electronics? This combination creates design complexities that require innovation in connector miniaturization due to space constraints, which effectively impacts temperature levels that must be addressed with clever and innovative design solutions and advanced predictive modeling.
Miniaturization and increased electrical content necessitate greater component density. Dissipating the same or more heat in a smaller space over the reduced surface area of miniaturized systems can create excessive heat risks that must be managed. Heat risks can increase if the electronics are in a sealed ECU and located in an area of the vehicle that sees extremes of ambient temperatures – such as under the hood. The harsh environment combined with high circuit density and small package size. requirements for next-generation connection systems can result in thermal challenges if not designed properly. Thermal issues in connectors can cause safety, reliability, and lifetime issues that must be addressed diligently at the design phase of a project. Molex executes high fidelity thermal simulation methods to drive design exploration and mitigate thermal issues before mass production. The traditional “build then test” approach of next generation connection systems is not efficient due to the cost and lead times of building test models. Thermal simulation provides immediate visibility, allowing for accelerated modification cycles, providing our customers with customized solutions to meet their needs from both a performance and longer-term production perspective.
Let’s (Not) Make Some Noise
With new technologies, comes new challenges. Traditionally, the internal combustion engine would dampen ambient noise generated from the road, tire, wind and vehicle structures. Without the engine to mask this noise, vehicle occupants can experience discomfort, decreased quality of conversations and drone-fatigue. Engineers can no longer rely on mechanical methods of noise dampening, such as sound deadening materials or lining the tires with foam, as these add cost and mass to a vehicle – which negatively effects energy consumption and range – two very critical parameters for EV’s.
Molex world-class noise cancellation sensors enable automakers to electronically control unwanted sound. Our accelerometer based Road Noise Cancellation sensor is strategically positioned on the vehicle chassis to monitor road noise, and in combination with intelligent algorithms, deliver a noise cancellation wave at the very moment the unwanted noise hits the occupants ears. Noise management technology is giving OEMs a wider range of noise reduction benefit – giving automakers a head-start in designing and deploying a lighter, higher-performing, more flexible, and more efficient solution for reducing unwanted noise.connectors can cause safety, reliability, and lifetime issues that must be addressed diligently at the design phase of a project. Molex executes high fidelity thermal simulation methods to drive design exploration and mitigate thermal issues before mass production. The traditional “build then test” approach of next generation connection systems is not efficient due to the cost and lead times of building test models. Thermal simulation provides immediate visibility, allowing for accelerated modification cycles, providing our customers with customized solutions to meet their needs from both a performance and longer-term production perspective.
The Road to Electrification is Bright
The continued increase of electrical content and the electrification of powertrains on vehicles is a positive and inevitable progression. It is important for experienced innovators, such as Molex, to support this megatrend by collaborating across the automotive ecosystems. To stay at the forefront of design requirements, reduce potential risks and develop solutions that fit the needs of this dynamic market. We are a leading supplier of electronics and connectivity solutions to most of the largest global OEMs and suppliers in the automotive industry. By ensuring our products, tools, and processes provide the automotive industry with dependable products. Providing guidance to allow our customers to design-in our solutions with confidence and helping to achieve a smooth and bright road to an electric future.
Visit Molex at TTI to learn more about Molex’s Vehicle Electrification.
from Charged EVs https://ift.tt/gbV9X2p
No comments:
Post a Comment