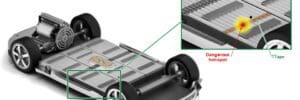
New technology platform enhances the performance and lifespan of EV batteries.
Lithium batteries offer the highest power density compared with other battery chemistries. Lithium batteries can store more energy in a smaller, lightweight package than any other type of battery. As a result, Lithium-based batteries are the battery type of choice for all types of electric vehicles. Unfortunately, lithium batteries have several downsides. They can undergo thermal runaway if damaged, under very high loads, overcharged, or exposed to high temperatures. Thermal runaway can generate enough heat to ignite the electrolyte and cause a fire or an explosion of a battery pack. Such conditions can severely damage the battery pack and the EV and potentially put the passengers at risk.
A new technology that mitigates the risk of battery thermal runaway is now available. The latest technology developed by Littelfuse, the TTape Distributed Temperature Monitoring Device, enables early detection of localized battery cell overheating. The innovative platform contributes to extending battery life and enhancing the safety of battery installations. TTape is a strip of tape with numerous closely spaced temperature indicators. Unlike a discrete thermistor, TTape adheres to battery cells and conforms to the shape of the cells, enabling high density monitoring of locations on a battery pack. The temperature indicating sensors quickly detect a cell hot spot preventing battery thermal runaway. With individual thermistors whose size limits the number of detection locations and prevents close spacing, a battery cell hot spot that is not near the location of a thermistor could rise to a dangerous level. TTape solves the problem of being unable to detect battery cell hot spots quickly.
This article introduces the reader to the benefits of the TTape Distributed Temperature Monitoring Device and details the product. In addition, a sample circuit illustrates usage in a protection scheme. Design engineers will find TTape an excellent and simplified component for ensuring lithium-ion batteries have maximum life and are safe to operate.
Description of TTape
TTape is a flexible, thin band of printed temperature indicators spaced closely together for maximum spatially resolved temperature monitoring. Its thickness is less than 500 µm which allows it to conform to any battery pack shape. Figure 1 shows the TTape strip with the printed temperature indicators (PTIs).
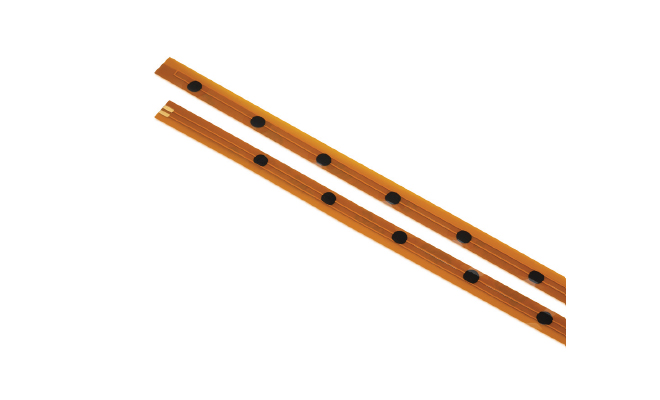
The printed temperature indicators are small dots of polymer positive temperature coefficient material. The PTIs are connected in series. When a PTI detects a temperature above the threshold level, its resistance increases by a factor of over 1000.
Figure 2 provides the dimensional details on the TTape Distributed Temperature Monitoring Device. Temperature sensors can be spaced around 10 mm apart. The TTape has options for a narrow width of either 8 mm or 10 mm and a standard length of 337 mm. Custom designs can be as long as 1 m. Pressure-sensitive adhesives bond the TTape to a surface. The adhesive allows bonding to metal, polyamide, PET, and polyimide surfaces.
A standard tape length of 337 mm includes ten printed thermal indicators. Custom designs can consist of up to 50 of the PTIs. The printed thermal indicators have a maximum diameter of 5 mm with a standard spacing of 30 mm. The narrow spacing between the PTIs allows increased spatial resolution for monitoring the temperature of all cells on the battery pack. Discrete temperature sensors cannot achieve such close monitoring of all individual battery cells. Furthermore, with a thickness of under 500 µm, the TTape can conform to the irregular surface of the battery pack and have direct contact with the individual battery pack cells.
The TTape connects to an electronic circuit with a 2-wire solder pad interface. Figures 1 and 2 show the two solder pads, and Figure 2 defines their function.
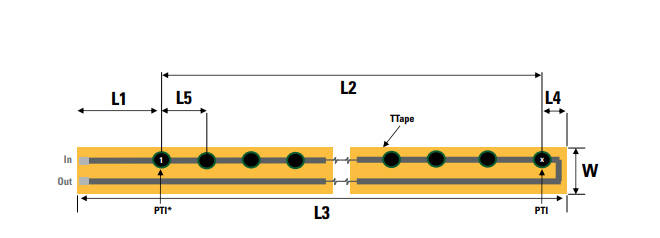

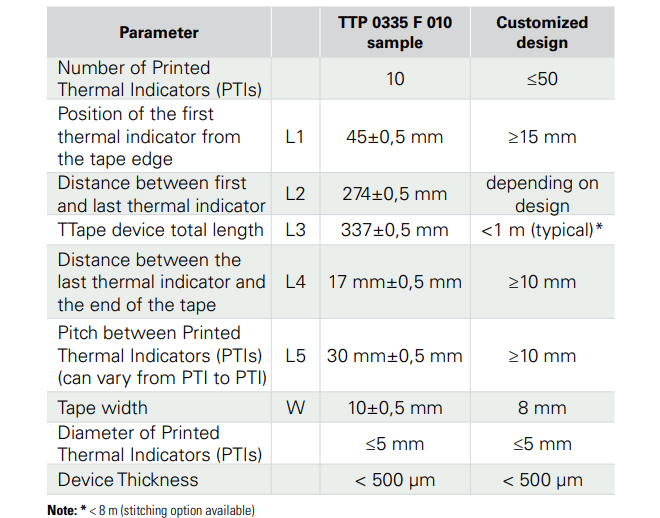
The TTape has a trip temperature setpoint of 58 ± 3° C for early overheating detection before a battery cell can reach a dangerous temperature level. Lithium-ion and other battery chemistries can charge and discharge at temperatures under 60° C before typical battery management circuits take action. The battery management system will interrupt the load or the charging power on the battery pack when a temperature above 60° C is detected. Generally, the 58° C setpoint tolerates the battery pack temperature fluctuations that occur when a battery pack is under load or re-charged. The printed thermal indicators have a response time of under one second. If a battery pack temperature exceeds the nominal 58° C threshold for longer than one second, the TTape temperature monitor will respond.
To avoid rapid on-off cycling near the threshold temperature, the TTape PTI material has a hysteresis characteristic which prevents wear on critical system components and avoids false alarms. This design approach ensures the system responds only when there’s a genuine overtemperature condition, contributing to the safety and durability of the battery pack.
Circuit implementation
TTape works in TTL-level l, 5 V circuits, or 3.3 V logic circuits. Figure 3 shows a recommended circuit configuration for use with a TTape monitor. VT is a logic high when the TTape printed thermal indicators detect a temperature exceeding 58° C and switch to a high resistance. VT is a logic low when the temperature is below 58° C or if the temperature has exceeded the threshold temperature and has fallen below 42° C. The printed thermal indicators exhibit a hysteresis effect of approximately 16° C once the threshold temperature is exceeded. The right side of Figure 3 presents the hysteresis curve of the TTape device.
The logic circuit is a simple circuit employing a recommended value of RP as 200 KΩ. VT can provide a signal to an A/D converter in a microcontroller. When the TTape is not detecting a battery hot spot, the 5 V circuit draws around 25 µA to consume only 125 µW. The TTape needs only one A/D input line on the microcontroller to transmit the temperature state of the battery cells. The microcontroller can either be a part of the battery management system or be an interface to it.
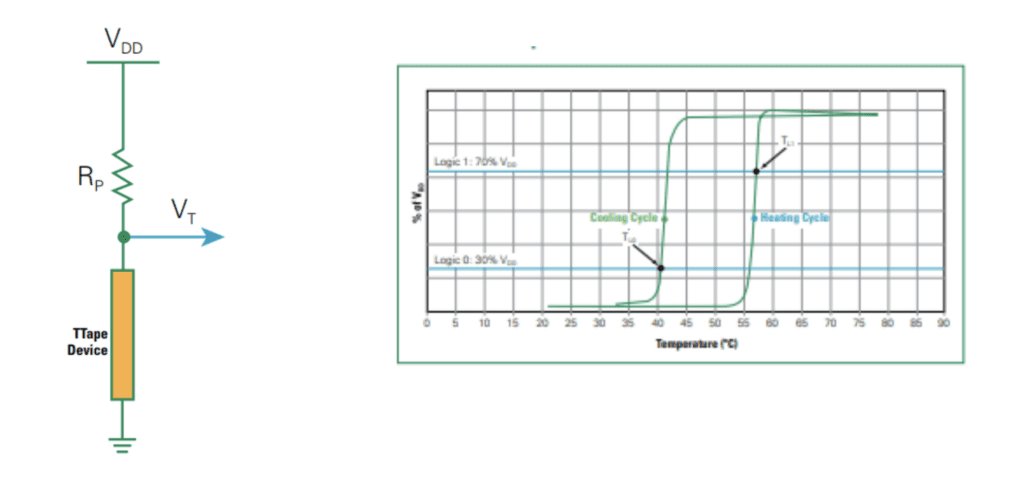
Comparison with discrete thermistor temperature monitoring
With only 30 mm between the printed thermal-indicating sensors and a thin adhesive tape form factor that can conform to any surface, the TTape can detect a battery cell temperature rise before a discrete sensor can unless the temperature rise is right under the discrete sensor. Figure 4 illustrates this situation. If a thermistor is one cell away from an overheating cell, it could take over two minutes for the thermistor to respond to the high temperature condition. With PTIs on each cell, the response is under one second.
Unlike a NTC sensor, the TTape temperature monitoring platform does not need calibration since it is essentially a two-state device. In addition, the electronics that process the TTape sensors do not require a temperature conversion calibration table.

As a conforming tape, the TTape consumes negligible space on the battery pack. TTape enables easy installation and allows monitoring of any battery pack construction. Figure 5 shows an example installation of a TTape monitoring strip on a battery pack.
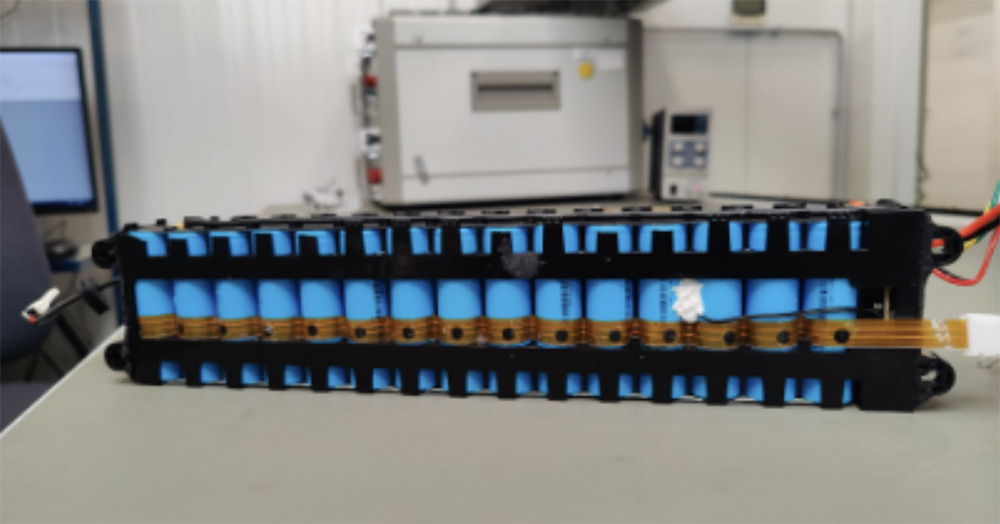
High-density monitoring for enhanced safety
The TTape Temperature Monitoring Platform presents designers with the unique ability to have highly compact temperature monitoring on each group of cells in an EV battery. The high-density monitoring minimizes premature aging by detecting and preventing temperature hot spots on individual cells or a group of cells. This low-cost, minimal space-consuming solution provides enhanced safety and extended battery cell life. Furthermore, the TTape monitoring device is AEC-Q200 qualified for use in automotive vehicles.
For more information on the TTape Distributed Temperature Monitoring Platform including installation details and circuit implementation, see the TTape Distributed Temperature Monitoring Device Application Note.
To obtain technical assistance, visit the TTape product page and contact Littelfuse at www.littelfuse.com.
from Charged EVs https://ift.tt/DihRITd
No comments:
Post a Comment