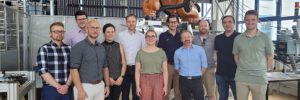
Researchers from Germany’s Fraunhofer Institute for Machine Tools and Forming Technology IWU have teamed up with partners in the COOLBat joint research project to develop next-generation battery enclosures for EVs.
The COOLBat project focuses on making lighter enclosures to reduce power consumption and increase driving range by combining individual systems, packing more functions into a smaller installation space and using new heat-conductive materials and bio-based flame-retardant coatings.
The researchers have explored combining individual systems in the enclosure that previously performed thermal and mechanical functions separately. The cooling unit function is combined with that of underride protection in a single component, the base plate.
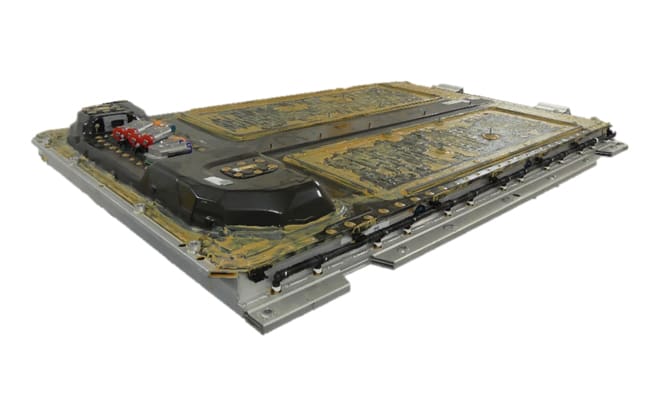
Aluminum foam inside the base plate absorbs the impact energy from stone impacts and accidents. Combined with a phase-change material (PCM), a kind of wax that can be used to store and later release thermal and cooling energy, the aluminum foam also reduces the amount of energy needed to cool the battery.
This configuration protects the battery cells from mechanical loads and overheating at once. A fluid flows through the channels, cooling the cells from below and from the sides. This reduces the electricity needed to cool the cells and eliminates the need for cooling elements elsewhere in the vehicle.
One of the aims of the project is to replace the heavy conductive pastes with ecofriendly heat-conductive materials to connect the battery module for thermal purposes. To do this, the researchers are using a plasma process to metallize open-pored reusable foams that are then placed in the spaces between the battery and enclosure in pad form.
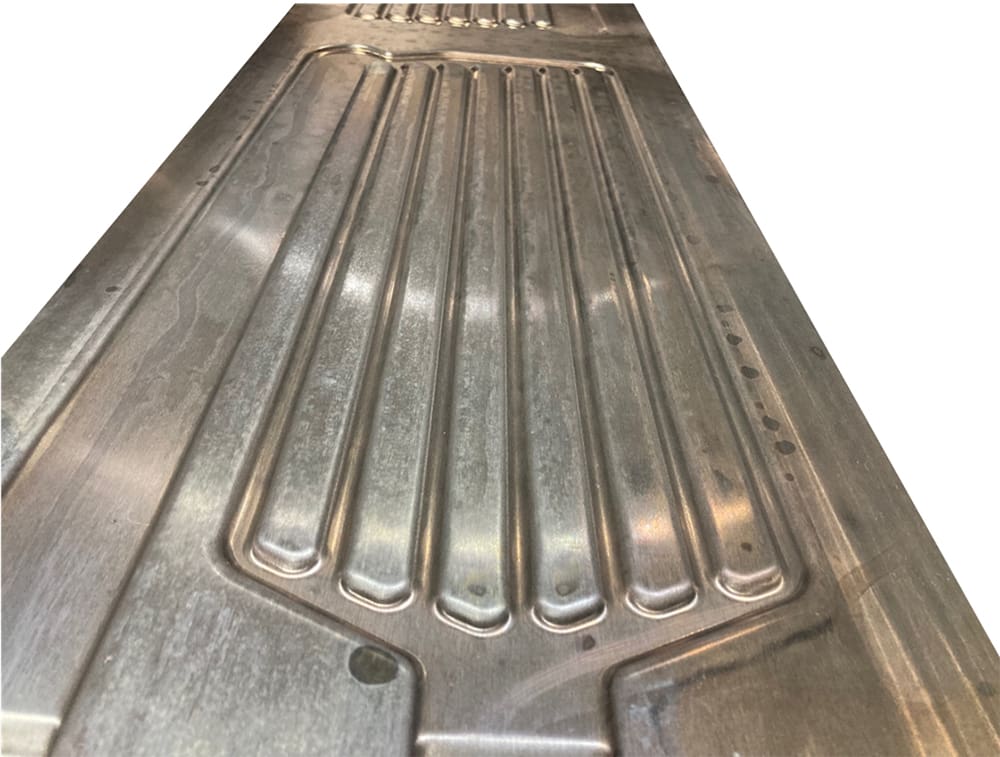
A new flame-retardant coating applied to the underside of the enclosure lid prevents fire from spreading from the battery cells beneath. The previous steel enclosure lid has been replaced with a new fiber composite lid, reducing the component’s mass and making it possible to reuse the lid.
The researchers are using the Mercedes-Benz EQS battery as a reference and technological demonstrator.
Future plans call for the project’s results to be extended to other applications and industries that use large batteries, such as in trains, aircraft and boats.
“We’re focusing on functionally integrated structures. Tasks that used to be handled by different modules inside the battery are being integrated into a single component—the base assembly, in this case—to shrink the installation space and streamline interfaces,” said Rico Schmerler, a project manager and scientist in the Battery Systems department at Fraunhofer IWU. “These base plates will provide protection from overheating and avert damage to the battery core in case of an accident.”
Source: Fraunhofer Institute for Machine Tools and Forming Technology IWU
from Charged EVs https://ift.tt/Oyb5v04
No comments:
Post a Comment