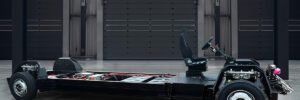
Taking the EV skateboard chassis to another level
- The so-called skateboard chassis is a staple of modern EV design. REE Automotive has taken this concept a step further by packaging the motor, steering, suspension and brakes into an independent module called a REEcorner that can be placed at any desired position on the skateboard platform.
- REE’s vehicles also use an innovative x-by-wire system—drive, steering and braking are all controlled electronically. This not only eliminates hardware such as steering racks, it also allows performance characteristics of a vehicle to be defined in software.
- REE’s platform includes both electrical and mechanical connection points to make it easy for upfitters to create an endless variety of vocational vehicles.
Q&A with Dr. Peter Dow, REE Automotive’s VP of Engineering.
To a large extent, vehicles are designed around their propulsion systems. The first generation of modern EVs shoehorned an electric motor and a battery into a vehicle that was designed around an engine, a transmission and a gas tank. It soon became apparent to vehicle designers that designing an EV from the ground up would deliver many advantages, including better handling and more space for passengers and cargo. When a certain American startup designed its second-generation vehicle, it put the battery pack on the bottom, in a flat platform. This arrangement, which has since come to be called a skateboard, is the basis of most modern EVs.
An Israel-based startup called REE Automotive has taken the skateboard concept a step further: since there’s no need for a longitudinal driveshaft or transmission, why not make the wheel assembly a modular component separate from the skateboard platform, so it can be placed wherever it’s convenient for the design of a particular vehicle? This allows almost unlimited flexibility in vehicle design—a huge advantage in the commercial vehicle market, where one size definitely cannot fit all.
The REEcorner integrates the motor, steering, suspension, braking and control into a single compact module. Each REEcorner is completely independent, and is controlled by its own electronic control unit (ECU). The REEcorners are attached to what REE calls a platform (and others might call a skateboard chassis), which contains the battery packs and other vehicle systems. REE’s x-by-wire system (drive-by-wire, steer-by-wire, brake-by-wire), which earned FMVSS and EPA certification earlier this year, controls all vehicle functions electronically. This eliminates driveshafts, control cables and other hardware vestiges of the ICE era, and allows performance parameters to be adjusted in software.
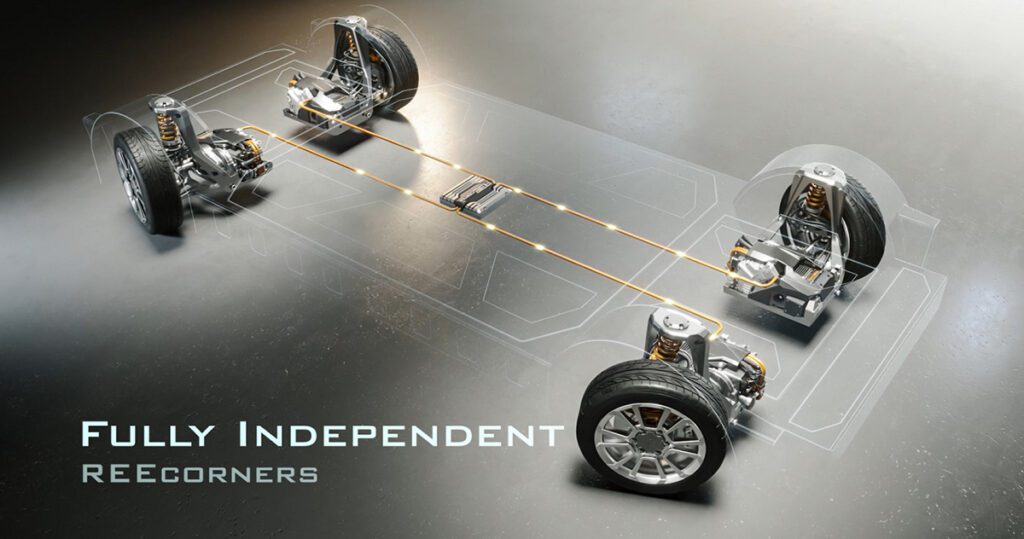
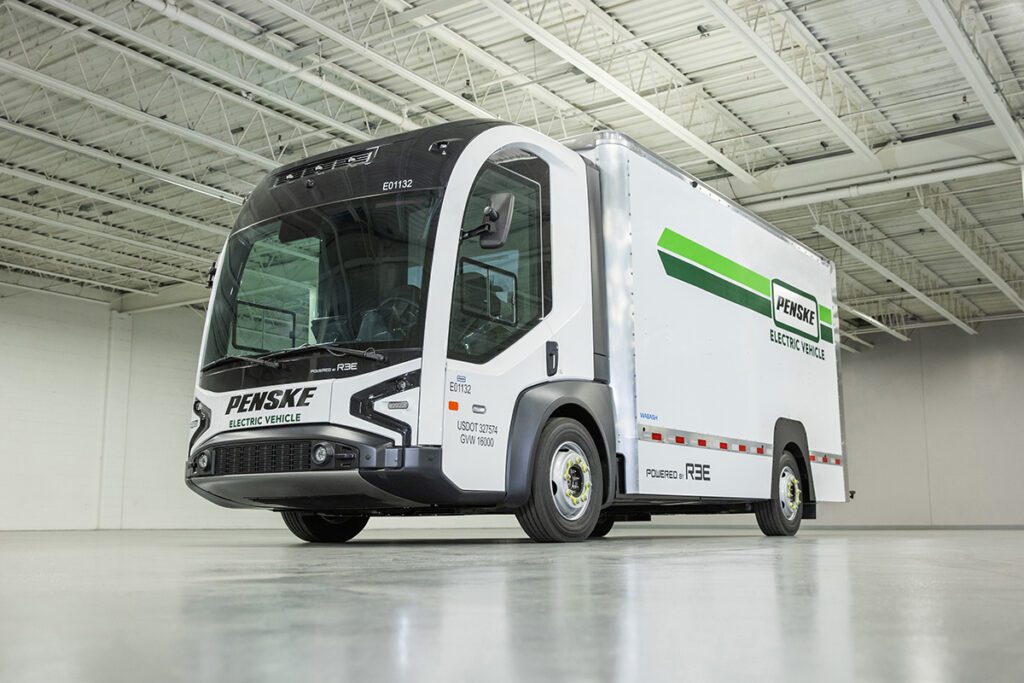
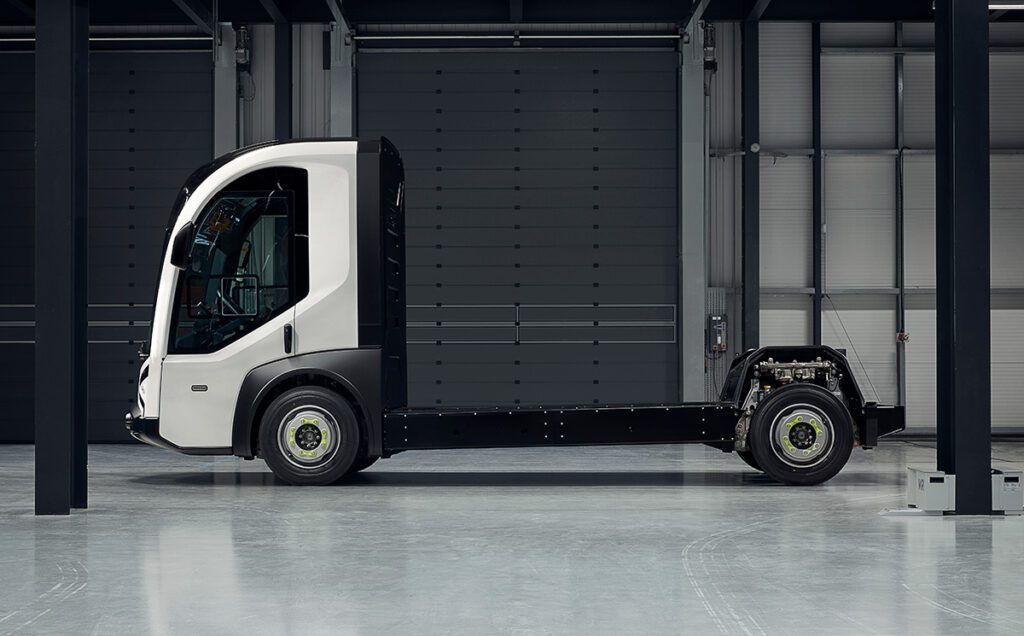
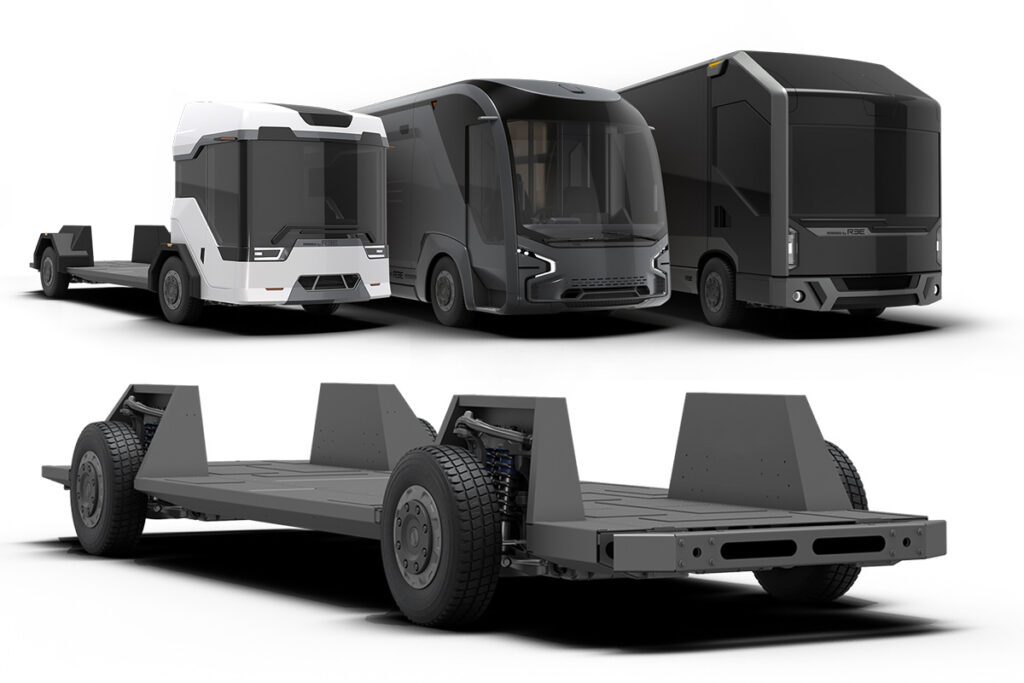
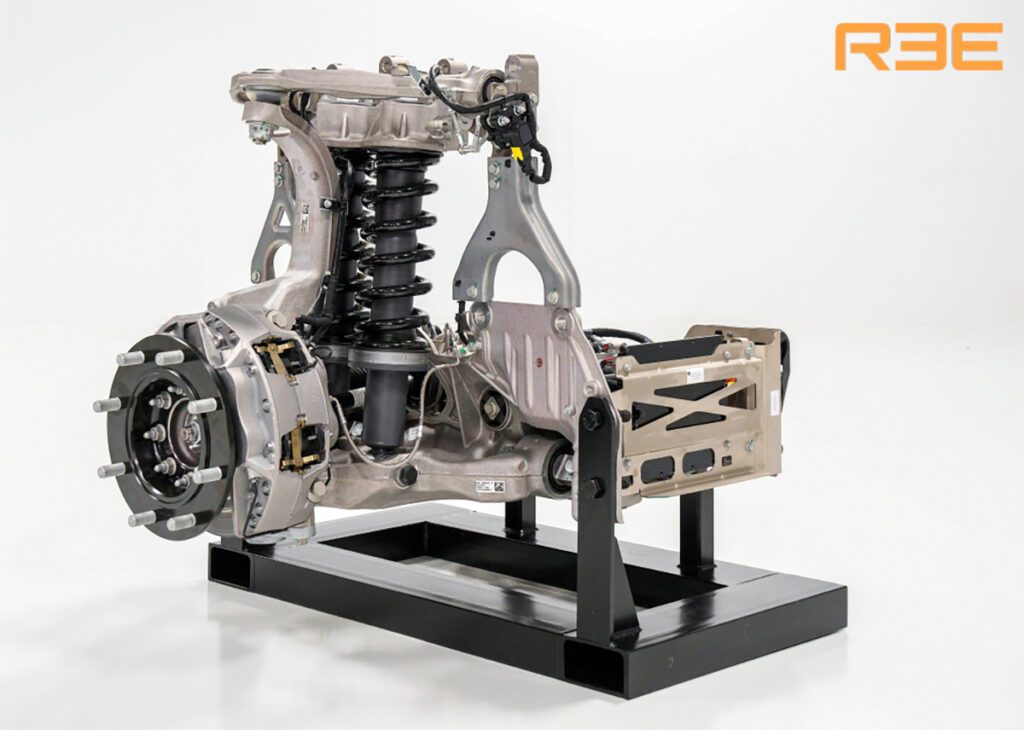
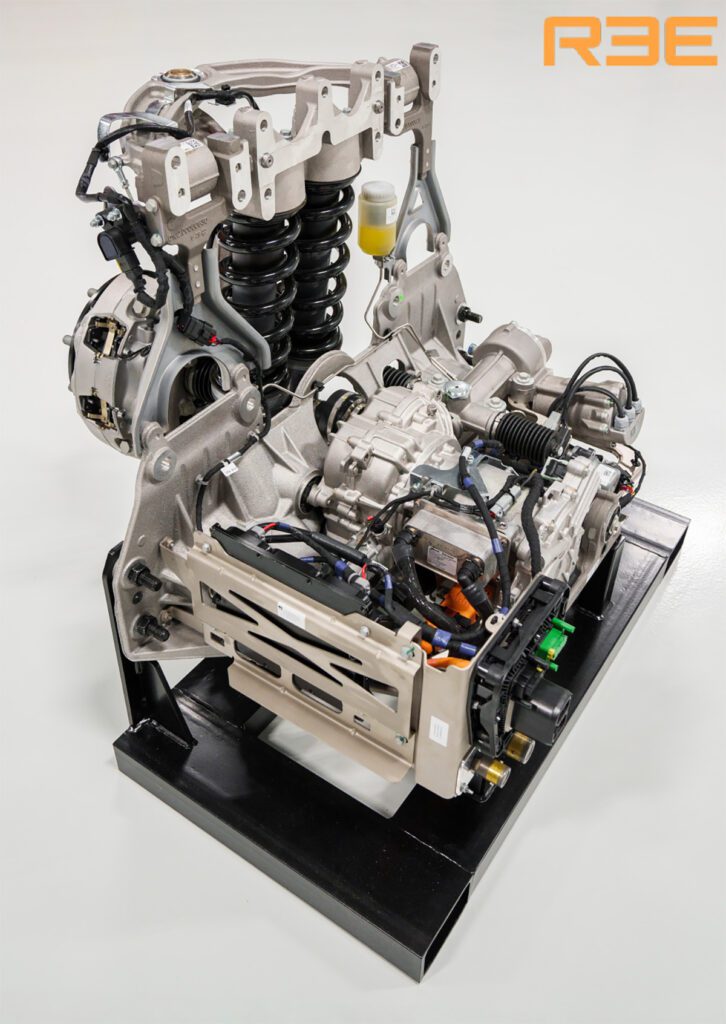
REE is setting its sights on the North American commercial vehicle market—the company currently has 78 sales and service locations in the US, and approximately $60 million worth of orders in its order book at last count. The company has begun customer deliveries of its P7-C electric demo trucks, and fleet heavyweights including Penske and U-Haul are evaluating its vehicles.
Charged spoke with Dr. Peter Dow, REE Automotive’s VP of Engineering.
Charged: What are some of the advantages of your modular design concept?
Peter Dow: Our corner can be used on each of the four corners of a truck. So there’s no left- or right-handedness, there’s no front or rear, and that gives you all the flexibility that is so important in the commercial vehicle market. We can change wheelbases reasonably quickly and easily for different applications, which means that customers haven’t got a massive investment in a platform. They can take the corners and position them in the optimum setup for their applications.
Charged: You’ve got basically two products—the corner and the skateboard chassis, which you call the platform. Does each of these come in just one variety, or are there different options?
Peter Dow: The corner comes in one variety, so it has one part number. We manufacture that as a unit that will fit a range of applications. We’ll do a Class 3, Class 4 or Class 5 truck with the one corner—the systems have been sized to apply to all of those different trucks. The platform is also a modular design, but it can be sized to meet different applications. So, we could position three of our battery packs in a truck to give you one wheelbase and a certain range, or we could make the wheelbase longer and put four battery packs in.
The corners are very much the building blocks. The rest of the components—the mechanical chassis, the batteries, the cooling systems—are designed to be flexible, to expand or contract to meet what customers need.
We can change wheelbases for different applications, which means that customers haven’t got a massive investment in a platform. They can position the corners in the optimum setup for their applications.
Charged: Each corner includes a motor, but this is not an in-wheel motor.
Peter Dow: No. The corner has an inside and an outside component, and the inside component has all of the drive mechanisms. We have a three-in-one electric drive unit (EDU) that contains the motor, the gearbox and the inverter, and there’s one of those in every corner.
We have a steering actuator, which operates on a 48-volt system, which controls the steering, so you get steering on all four corners, both front and rear, which is another benefit. We also have a brake actuator that controls your brake pressure. We have a hydraulic brake system—fairly conventional—but the electrical actuator that controls it sits within the corner. All that—drive, braking and steering—is controlled through the electronic control unit (ECU) that sits in the corner.
If you need to replace a corner, it’s a very simple operation of a few bolts to replace it with a new unit and have the truck operational again. We’ve shown examples of replacing that whole corner within an hour.
Charged: You have an electric truck for sale now, but you can also work with customers to custom-design vehicles for their specific applications.
Peter Dow: Yeah. We’ve got a network of dealerships in all the key states that we want to be operating in within the US. They’ll be offering a standard product—our P7-C, a Class 4 chassis cab—as a starting point. It has a single wheelbase as an application to show the different kind of boxes, platforms, etc, that can be upfitted to that. We’re also working with other customers on different ideas—maybe a longer-wheelbase version, maybe a kind of walk-in van.
For the customers, we’re looking at what they need in terms of volume, weight capacity and maybe EV range. For some, range is a critical part, so we can look at optimizing the battery packs for them. For some, the weight capacity is critical, and we can optimize the vehicle for that. We have an ability to listen to our customers, understand what they want, and then easily modify the end product.
Charged: The platform can be upfitted to create just about any kind of vocational truck, right?
Peter Dow: Correct. We’ve been working closely with a number of upfitting partners and trying to make it so that you can put different applications onto our truck. One of the benefits of the REE system is that we’ve got a very low platform, but we also have the ability to build what we call a high-floor application, so you can go to the conventional dock heights that you normally get with a box truck. Within the chassis design, we’ve put in connection points for both the electrical and mechanical upfitters, so it is very much an easy application for them to use. The upfitters have given us some really positive feedback that it’s been an easy truck to work with.
The upfitters have given us some really positive feedback that it’s been an easy truck to work with.
Charged: Do you have some prototypes out there of different types of trucks?
Peter Dow: Yes, we have a number of trucks in the US within our dealer network that have different configurations on them.
What we want to do is to get people driving our trucks, and one of the messages we want to get across is that our by-wire system is designed to give a lot of benefits in terms of the drivability of the trucks. We’ve had a lot of feedback from people that have driven our trucks. At ACT in Las Vegas, we had numerous people driving the truck on the ride-and-drive event, and the feedback was that it’s more like driving an SUV, not like driving a Class 4 truck. You can actually control the feeling of the steering wheel, the feedback you get. We’ve got four-wheel steer, so the maneuverability at low speeds is really high.
Charged: So, the drive-by-wire system allows you to customize the driving feel of the truck?
Peter Dow: Absolutely. Conventionally, in a lot of trucks you look at maybe putting some customization into the throttle, you could maybe change the acceleration profile, but we can look at the amount of steering feedback and the amount of rear steer that we’re bringing in. At the moment, at low speeds we bring in the rear, so it gives you a lot more maneuverability. At higher speeds we take the rear steer out. We can tune that to what customers want. We can also do things like change the amount of regeneration we have from the electrical motors. It’s very easy for us to change things because it’s a software change, not a hardware change.
Charged: So maybe one customer likes a Ferrari feel and another customer prefers BMW-like handling.
Peter Dow: Exactly. For example, if we had one customer that was a bakery, maybe he wouldn’t want the Ferrari because he doesn’t want to squash his cakes. Somebody might want to have a very gentle acceleration profile because he’s got goods in the back that he wants to protect.
Charged: And somebody else might want plenty of acceleration because they want to get to the next job fast.
Peter Dow: Absolutely. That’s the ethos of understanding what the customer wants, and within reason, we can provide whatever they need.
It’s very easy for us to change the driving feel of the truck, because it’s a software change, not a hardware change.
Charged: How many of the components do you manufacture in house? I know you work with a lot of Tier 1 suppliers.
Peter Dow: Yes, we do. We own all the design. We tend to use our supply chain to do the main manufacturing activities, and we do an assembly process. We assemble the corners here in the UK. We have what we call our Integration Center, which is our robotic assembly line for the corner. And that takes some systems and some pre-assembled manufactured parts, and assembles that into the full corner. Then we use contract manufacturers to assemble the rest of the truck in terms of putting the components together.
We’ve designed everything, and I’ve actually gone through a number of iterations of design. For example, the corner design itself, we started three years ago and since then, we are probably on the fourth iteration in terms of optimization. We’ve just finished a long-term durability test on the corner, where we’ve actually simulated a 20-year usage. So we know that we’ve got the durability that is going to be needed out there.
Charged: What can you tell us about your suppliers? Who’s making the motors and the battery packs?
Peter Dow: We have a number of options. At the moment, we have two different motor suppliers, and the same for our steering system and our braking system. We won’t go into details of who they are, but we don’t want to be constrained to one supplier because there’s always a risk associated with using one supplier. Same with our high-voltage battery—we’ve designed the system so that we can have different battery packs installed into our chassis, so we are not constrained to one supplier.
We want to be agnostic so that we can go with different suppliers. Some customers say, “We want to use certain battery packs, or we’ve got an association with a certain supplier we want to use.” We’ve got our supply chain in place, but we want to have that flexibility as well.
Charged: Tell me more about your modular battery pack. The customer can select different sizes. Can they also select different chemistries or different formats?
Peter Dow: Again, we’re pretty agnostic to the chemistry and the battery pack itself. At the moment we have a modular system based on essentially NMC Li-ion 42.8 kWh battery packs. In our P7-C application, we have three packs, which gives us 128 kWh total capacity for the truck. But we can look at replacing that with different options. We can also look at other power sources if need be, because all we worry about is making sure we have 400 volts going to our corner system. We’ve always had a design philosophy of being power source-agnostic. We can look at different battery cells, or even a range extender.
Charged: So you could add a gas or diesel engine if a customer wanted that.
Peter Dow: Yes, if the customer decides.
We’ve always had a design philosophy of being power source-agnostic. We can look at different battery cells, or even a range extender.
Charged: Tell me more about the charging.
Peter Dow: The platform is broken down into what we call five zones. Zone one at the front has all of the cooling system: pumps, radiators, compressors, etc. Zones two and four actually house the corners. And then zone three in the middle has the batteries, the DC-DC converters for the 12-volt system on the truck, the 48-volt system for our control system. It also has the onboard charger, which can support both AC and DC charging. At the moment, we support 22 kW AC charging and up to 140 kW DC charging.
Charged: We’ve written about different kinds of motors, and we’ve had experts describe the pros and cons of different kinds. What kind of motors do you like? Do you see using different ones for different applications?
Peter Dow: Our initial application is a high-speed induction motor. We’ve got about a 22-to-1 ratio on the gearbox. We’ve got a lot of innovation in the rest of the truck, but we wanted to keep the motor technology kind of as established as possible. We don’t need to do anything special with our motors for the application we’re looking at, as long as we’ve got decent efficiency. We also have an application with a permanent magnet motor.The ability to be able to flex between different motor types in the future is something we believe would be helpful.
Charged: Give me a brief history of the company and your background.
Peter Dow: I’ve been working in automotive new product development for 30 years. I’ve worked across a number of global automotive consultancies, technology startups and Tier 1 suppliers, including Lotus Cars, Geely Auto, Ricardo Technical Consultancy, Getrag Transmissions and Tata Group.
I joined REE 3 years ago. REE has been active for about 10 years in different forms, and came out of stealth mode about 4 years ago. I came in to help build the engineering activity.
We’ve got a team of about 150 people here in the UK working on mechanical engineering, vehicle engineering, and some software engineering. We do all our vehicle tests and development work here, but we also work very closely with the team in Israel that are doing a lot of the electrical system development, the software development. We’ve also got a team in the US that are looking at after-sales and sales support.
We’re selling just in the US at the moment. We’ve got our development here in Europe, and we are looking at other markets, but we’re very much focused on the US at the moment.
Charged: We’ve seen a lot of commercial EV companies come and go. Is there anybody out there that’s offering the kind of thing that you are?
Peter Dow: In some ways, we feel we’re a bit of a last man standing, and we are quite proud of that because we’ve been really clear on what we want to deliver. Because we’ve got our by-wire and our corner technology, we are very different. When we go to the trade shows, we never really look around because we don’t think we’ve got any direct competition. It’s not something that distracts us. We just carry on and stay focused on getting our first product out there, the P7-C.
from Charged EVs https://ift.tt/qxLtd2r
No comments:
Post a Comment