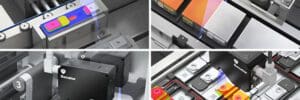
The increase in demand for EV Batteries has already permanently transformed the car manufacturing landscape, with almost all major automotive companies now operating electric vehicle production lines.
While electric vehicles do have less moving parts than their internal combustion engine (ICE) counterparts, manufacturing them is still extremely complex. From stators and rotors, to intricate wiring harnesses, LMI is involved with many EV manufacturing applications. But the heart of an EV is its battery, and this is where machine vision solutions have become essential to market success.
EV Battery Manufacturing Overview
EV battery manufacturing can be broken up into 5 general steps: (1) electrode manufacturing, (2) cell assembly and packaging, (3) cell-to-module assembly, (4) module-to-pack assembly, and (5) final installation inspection.
Gocator 3D smart sensors and their built in, onboard measurement tools are used in every stage of this manufacturing process.
Let’s look at these applications individually.
Electrode Manufacturing
Electrode slurry is coated onto copper and aluminum foil to facilitate electric flow. The metal surface, separator, and coating must be inspected for edge defects as well as uniform shape and thickness.
During this step, Gocator sensors are used to ensure uniform shape and thickness of the electrode as the slurry is applied. Sensors are also used to measure the distance between tabs on a cell sheet. Tolerances are extremely small for these applications so high resolution and small field of view sensors are used.
Smart 3D sensors are used for different tasks at this phase of inspection including:
- Electrode Width Gauging – Accurate width gauging of the dimensions of the separator and electrode.
- Electrode Edge Profile Measurement – High-speed profiling of the edges of coated electrode sheets to ensure the correct dimensional tolerances are met.
- Tab Distance Gauging – Scanning and measurement of the distance between tabs on a cell sheet to meet dimensional tolerances.
Cell Assembly and Packaging
A separator and electrode are joined together, and the joined cell (including anode and cathode) is either wound, rolled, or stacked. Stacked cells are then housed in a metal casing and sealed by welding.
Two of the most common cell types used in electric vehicles are cylindrical and prismatic. Cylindrical cells are packed together into groups and scanned for presence/absence, correct position and dimensions, as as well as for potential surface defects such as any dents or scratches on the cell top. Only 3D provides the shape (height) data required to inspect battery surface features and dimensions for defects such as bulges, fissures, warps, and more.
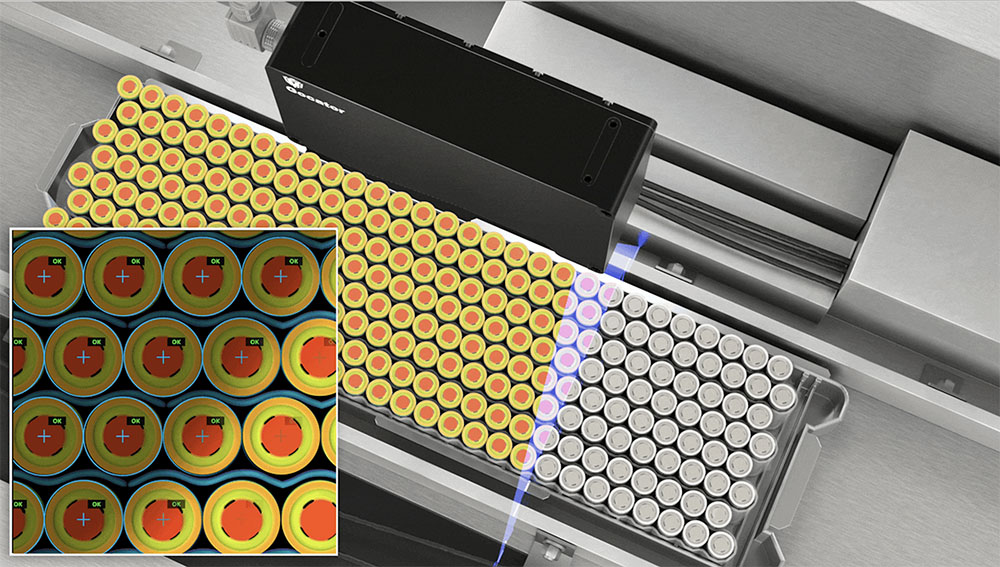
Prior to welding, a Gocator® or multisensor network delivers high-speed 3D laser profiling and a built-in tool to measure the gap & flush between the prismatic battery cell and its metal casing. After welding, they are inspected again to ensure that the weld seam is uniform and within tolerances.
The surface of the battery cell needs to be inspected for correct dimensions and to detect defects of the face, edges, and corners. It is also worth noting that smart 3D sensors like Gocator come with blue laser model options. The shorter-wavelength blue light generates higher-quality scan data (i.e., less noisy) on highly specular battery surfaces such as polished metal.
Cell-to-Module Assembly
Once the individual battery cells are inspected for quality control, a set number of them are precisely grouped together to form a battery module. An example application for module inspection is for sensors to measure and inspect the weld seams of each module.
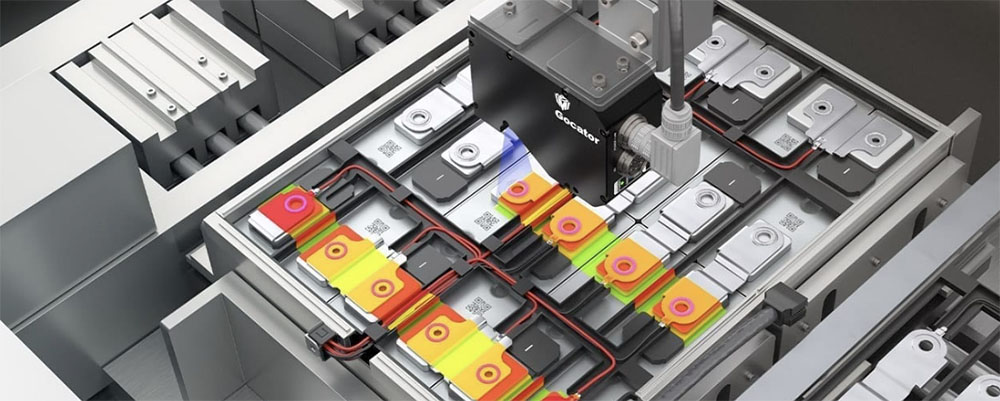
Module-to-Pack Assembly
Modules are then combined to form battery packs. Gocator sensors are used at the final stage of the process, combining modules into a single battery pack, ready to be installed into a new electric vehicle. It is necessary to measure and inspect its length, width, height, and flatness of each surface to ensure that all dimensions are matching the GD&T design tolerances.
Final Installation Inspection
In electric vehicles, a large tray/pan sits underneath the floor panel. The lithium-ion battery pack is glued to this tray. Gocator sensors are used at this final stage to inspect the glue bead application for correct dimensions (height, volume, width, length) and surface quality (breaks, gaps, overflow etc.).
Choosing the Right 3D Sensor for Your EV Battery Application
LMI Technologies offers a range of laser profile sensors that can handle any EV battery inspection application. For example, the Gocator 2500 Series offers ultra high-speed blue laser profiling for high-performance inspection of shiny EV battery surfaces. Or when even greater measurement precision is required, engineers can deploy the Gocator 2600 Series in their production lines for powerful ultra high-resolution 4K+ profiling.
Combine Smart 3D Scanning with AI-Based Inspection
In addition to its suite of high-speed, high-resolution 3D smart sensors for EV battery scanning (with web browser interface and onboard software), LMI Technologies also provides inspection engineers with the option to add powerful FactorySmart AI-based inspection to their EV Battery production lines for the most complete end-to-end solution on the market today.
For example, in EV battery array inspection, engineers can deploy a set of tightly integrated LMI products from sensor hardware to edge devices and human-machine interface (HMI) in order to solve the application with maximum performance and cost-efficiency.
An example of this solution might include:
- 2x Gocator 2600 laser profilers for 4K+ high-resolution 3D point cloud generation of the EV battery array
- 2x GoMax NX edge devices for sensor acceleration and powerful AI-based surface defect detection
- GoFactory interface for data management (performance monitoring, telemetry dashboarding, configurable alerts)
Conclusion
EV battery production continues to grow rapidly around the world. LMI is not only supporting the current industry, but actively developing next generation sensors specifically designed to meet future battery production needs.
For more information visit our EV Battery Industry web page.
from Charged EVs https://ift.tt/xzHYpfK
No comments:
Post a Comment